Los filtros prensa se utilizan en varios sistemas de procesamiento de fabricación de productos y también para gestionar de forma eficiente las separaciones de materiales de desecho. Es posible que se los requiera para recuperar agua u otras soluciones del flujo de proceso o desecho y/o para producir o recuperar materiales sólidos desaguados. Debido a que los filtros prensa se utilizan de forma tan extensa en las industrias, se encuentran disponibles varias opciones de equipos.
Estas son algunas de las opciones más comunes que se deben considerar al seleccionar un sistema de filtro prensa.
1. Diseño de placas de filtros prensa
Cuando se utilizaron por primera vez los filtros prensa hace varios años, estaban compuestos de una serie de marcos rectangulares sencillos intercalados entre placas sólidas planas con canales o ranuras en las superficies de la placa para permitir la eliminación del líquido. Aquí es donde se originó el término "filtro prensa de placa y marco". El material sólido acumulado en las telas de filtrado quedaba retenido entre el marco y las placas planas. Cuando no se podía bombear más material hacia el área del marco, las placas se separaban, lo que permitía que el material sólido cayera de los marcos.
El diseño de prensa de estilo de placa y marco está plagado de problemas en lo que respecta a eliminar el material sólido desaguado del marco. A pesar de que los diseños de prensa y marco aún se siguen utilizando en varias industrias/aplicaciones, en la actualidad, la mayoría de los sistemas de filtros prensa utilizan diseños de placa empotrada o placa de membrana.
Placas de filtrado empotradas
Las placas empotradas tienen superficies deprimidas dentro del área del perímetro de la parte frontal de la placa, lo que elimina la necesidad de que exista un marco. Las telas filtrantes están instaladas en las superficies de las placas. Cuando una serie de estas placas se mantienen bien juntas, se crean espacios vacíos entre ellas. Se utiliza una bomba para forzar el material de pulpa sólido y líquido entre las placas, donde el material sólido se captura en los espacios vacíos empotrados y el líquido pasa a través de la tela y se descarga a través de los puertos en la estructura de la placa.
Filtro prensa de membrana
Similar a las placas empotradas, las placas de membrana ofrecen un medio adicional de separar los materiales sólidos y líquidos que se pueden comprimir. La placa de membrana está empotrada, pero las superficies de la parte frontal de la placa son flexibles, lo que les permite expandirse hacia el espacio vacío creado entre las placas.
Similar a las placas empotradas, el desaguado se produce inicialmente bombeando material sólido y líquido entre las placas. Una vez que no se puede forzar más material hacia los espacios vacíos de la placa, se detiene la bomba. La superficie de la placa de membrana flexible luego se expande con agua o aire comprimido, lo que fuerza la superficie de la placa flexible hacia el material desaguado. A medida que se expande la superficie de la placa, se comprime el material sólido acumulado, lo que permite una eliminación adicional del líquido.
2. Diseños de vigas de apoyo para placas de filtros prensa
Otra opción de filtro prensa básico está relacionada con cómo se apoyan las placas de filtrado. Existen dos diseños básicos: la viga superior y la viga lateral.
Los filtros prensa de viga superior permiten apoyar las placas de filtrado desde vigas superiores. Este diseño permite un acceso completo a ambos lados y a la parte inferior de las placas de filtrado. Elimina cualquier interferencia en los residuos sólidos desaguados que caen de la prensa y permite el mejor acceso para la limpieza y el mantenimiento de la prensa. Además, el mecanismo que separa las placas de filtrado en una prensa de viga superior está generalmente alojado por encima del filtro prensa. Esto reduce la contaminación de los equipos provocada por los materiales que se están desaguando, lo que permite optimizar los costos de mantenimiento de los equipos y su vida útil.
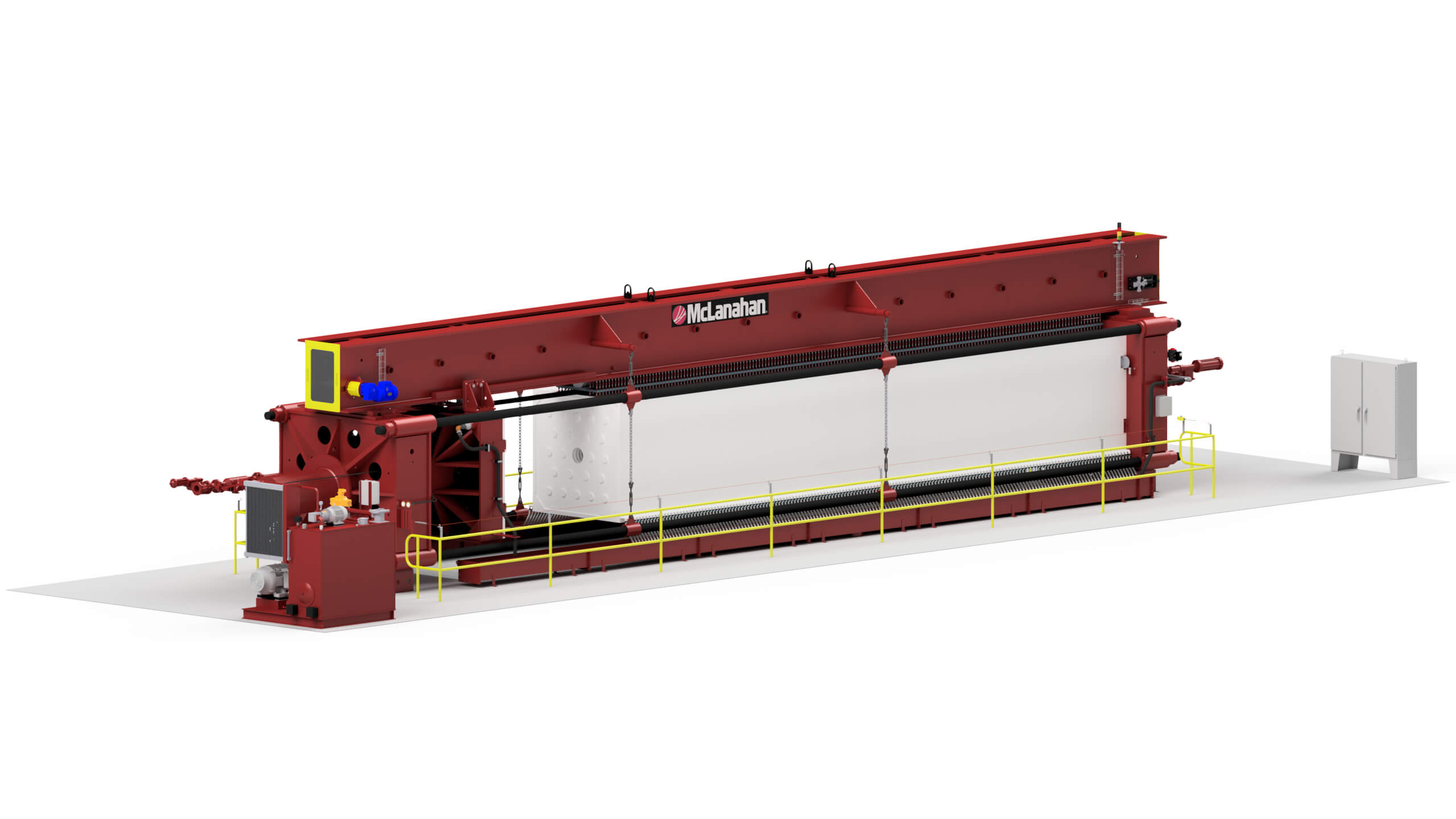
En un diseño de viga lateral, las placas de filtrado están apoyadas por vigas largas a cada lado del filtro prensa. Gracias a este diseño, el mecanismo de apertura de las placas se logra mediante el recorrido del cilindro de compresión hidráulico principal o mediante un mecanismo independiente de apertura de la placa colocado en las vigas laterales. En ambos casos, las placas están unidas entre sí con cadenas cortas o enlaces mecánicos, lo que permite que se abran varias placas con un solo movimiento. El diseño de viga lateral generalmente se utiliza en aquellos casos en los que los filtros prensa tienen suficiente capacidad y en los que las limitaciones de espacio restringen el tamaño de los equipos. El diseño de viga lateral también permite un acceso abierto por encima de la pila de placas para la sustitución de las telas y el mantenimiento de las placas.
3. Opciones de descarga de agua filtrada
El líquido (filtrado) extraído durante el desaguado en un filtro prensa pasa a través de las telas filtrantes colocadas en la superficies de la placa y sale por la placa a través de los puertos o canales internos. En las placas con descarga de filtrado de diseño cerrado, el líquido pasa desde la superficie de la placa hacia puertos pequeños en dos o más esquinas de la placa.
Desde allí, cada placa tiene un orificio en la esquina fresado por todo el espesor de la placa. Con las placas unidas entre sí, estos orificios en las esquinas actúan como un trayecto de tubería para que el agua filtrada salga por uno o ambos extremos de la pila de placas, a través de las placas estructurales del filtro prensa. Las tuberías colocadas en las placas estructurales fijas y/o móviles dirigen el líquido hacia un tanque de recolección de filtrado o hacia un tanque espesador/clarificador.
Otra opción para eliminar líquido de la prensa se denomina "descarga de filtrado de diseño abierto". En este caso, cada placa de filtrado individual tiene un puerto interno en ambas esquinas inferiores, lo que permite que el líquido se descargue directamente desde cada placa a una artesa de recolección o directamente a una bandeja de goteo ubicada debajo del filtro prensa.
La descarga de filtrado de diseño abierto permite que el operador observe visualmente la cantidad y la limpieza del líquido que se está descargando de cada placa. Cuando una tela de filtrado está dañada o con un desgaste excesivo, saldrá un líquido muy sucio por la prensa, y la descarga de filtrado de diseño abierto permite que el operador determine inmediatamente la ubicación de la tela dañada.
4. Bombas de alimentación de los filtros prensa
Todos los filtros prensa se alimentan mediante un cierto tipo de bomba de alimentación de pulpa para forzar los sólidos y los líquidos hacia los espacios entre las placas de filtrado. La presión creada por la acción de bombeo crea la fuerza necesaria para separar los líquidos y los sólidos. La bomba de alimentación de pulpa más común es la bomba centrífuga. Se puede utilizar una o más bombas centrífugas de una etapa en serie o bien una sola bomba centrífuga de múltiples etapas.
También es común el uso de bombas de desplazamiento positivo para la alimentación de los filtros prensa. Se puede utilizar una bomba de desplazamiento positivo individual o una bomba de desplazamiento positivo en serie con una bomba centrífuga. Los equipos de bombas utilizados determinarán la presión y flujo máximos de la pulpa que se alimenta al filtro prensa. Las bombas centrífugas de múltiples etapas o las bombas de desplazamiento positivo pueden generar más de 400 PSI y varios miles de galones por minuto de índice de flujo. Las presiones y flujos más elevados generalmente aumentarán la capacidad del filtro prensa.
5. Características de soplado doble y soplado de núcleo
Los filtros prensa pueden alimentarse desde uno o dos extremos con tuberías de alimentación de diseño apropiado. Los filtros prensa más grandes con más de 50-100 placas de filtrado requieren un flujo más grande de pulpa durante el período de filtración inicial. La alimentación de la prensa desde ambos extremos permite reducir el tiempo de filtrado de la prensa, por lo que la prensa puede llenarse más rápidamente. La alimentación doble reduce la cantidad de desgaste en las telas filtrantes, lo que extiende la vida útil de la tela.
Cuando una prensa está diseñada para alimentar a ambos extremos, también es posible completar un "soplado de núcleo". Al final de la etapa de filtrado, cuando se detiene la bomba de alimentación, la pulpa húmeda permanece en el orificio del núcleo de cada placa. Se completa una secuencia de soplado de núcleo para extraer la pulpa de núcleo restante antes de que se abran las placas de filtrado, lo que evita que la pulpa húmeda se descargue con los residuos desaguados.
El soplado de núcleo se completa mediante el uso de un conjunto de válvulas automáticas conectadas a las tuberías de alimentación de pulpa. La pulpa se expulsa a la fuerza del orificio del núcleo con agua presurizada y/o aire comprimido. El agua y/o aire comprimido se alimentan a un extremo de alimentación de la prensa, y la pulpa se expulsa a la fuerza desde el lado opuesto de la prensa, generalmente de nuevo al tanque de pulpa.
6. Limpieza de las telas filtrantes y bandejas para recoger el goteo
El medio de la tela filtrante permite que las partículas sólidas se capturen entre las placas de filtrado a medida que el líquido pasa por el medio de filtrado. Con el paso del tiempo, todas las telas comienzan a contaminarse con una cierta cantidad de material en la superficie y también en los espacios entre el tejido de la tela. Finalmente, la acumulación de material en las telas incidirá en el índice de filtrado y en la capacidad de sellar las placas juntas hasta el punto en el que será necesario reemplazar la tela.
La velocidad con la que se produce la contaminación depende en gran medida de las características (tamaño, distribución, forma, composición, abrasividad, adhesividad, etc. de las partículas) del material que se está desaguando. Se puede extender la vida útil de las telas con cierta limpieza periódica.
La limpieza manual de las telas con agua es la forma más común y sencilla para extender la vida útil eficiente de las telas filtrantes. Se utilizan mangueras simples de fuerza manual con presión y volúmenes medios para eliminar las acumulaciones en exceso de las superficies de las telas filtrantes, especialmente en las áreas de sellado y pernos de fijación. Los sistemas de lavado de telas totalmente automatizados, tal como se muestra en el siguiente video, pueden utilizarse para limpiar toda la superficie de la tela de forma efectiva, así como para eliminar parte del material de contaminación dentro del tejido de la tela. Estos sistemas de lavado utilizan duchas de limpieza de alta presión que están colocadas automáticamente para cada placa de filtrado y pueden programarse para limpiar periódicamente las telas en intervalos o ciclos definidos.
Las bandejas para recoger el goteo son grandes paneles móviles instalados debajo del filtro prensa para capturar el agua de limpieza durante el lavado de las telas. El movimiento de las bandejas para recoger el goteo hacia la posición hacia arriba o abajo generalmente se realiza mediante cilindros hidráulicos. Cuando la bandeja para recoger el goteo está en la posición elevada, el agua de la ducha de limpieza se dirige a una artesa de recolección, donde es posible reciclarla. Cuando las bandejas para recoger el goteo están en la posición hacia abajo o en la posición abierta, los residuos desaguados pueden descargarse fuera de la prensa al área de almacenamiento o hacia una cinta transportadora.
7. Secado y lavado de los residuos
Ciertas aplicaciones del filtro prensa requieren la mayor eliminación de líquido que sea posible o requieren la descarga de residuos sumamente secos. Similar a un escurrimiento con placa de membrana, el secado de los residuos se utiliza para eliminar más líquido del material sólido después de que se haya completado la etapa de filtrado con la acción de bomba de alimentación. Después de que la bomba de alimentación se haya detenido, las placas se mantienen bien juntas mientras se aplica aire comprimido entre las placas de filtrado. El aire comprimido pasa por el material sólido capturado entre las placas y extrae el líquido adicional de la prensa.
Las placas empotradas y las placas de membrana pueden utilizarse para completar la etapa de secado de los residuos, pero las placas tendrán puertos adicionales para dirigir el aire comprimido a través del material de los residuos.
Algunas aplicaciones de filtrado requieren la eliminación adicional del material soluble del material desaguado sólido capturado entre las placas. En este caso, el líquido, como el agua limpia u otros solventes, se bombea hacia el filtro prensa para eliminar los materiales adicionales de los residuos de filtración. Similar al secado de los residuos, el lavado de los residuos se realiza mediante el uso de placas empotradas o de membrana con puertos que dirigen el líquido a través de los residuos después de que se hayan formado mediante la acción de filtrado por bombeo. Una vez que se haya completado el lavado o secado de los residuos, el filtro prensa se abre para permitir que los residuos se descarguen antes de que se inicie otro ciclo.
Considerar estas 7 opciones clave de los filtros prensa por adelantado le ayudará a tener una mejor idea de cuál será la mejor para su aplicación. Si necesita asistencia, comuníquese con McLanahan.