Myth: Plate and frame describes all types of plate Filter Presses
The term “Plate and Frame Filter Press” is frequently used to describe modern plate Filter Press dewatering technology.
Flat surface plate and frame
The plate and frame Filter Press was one of the earliest types of plate Filter Press designs.
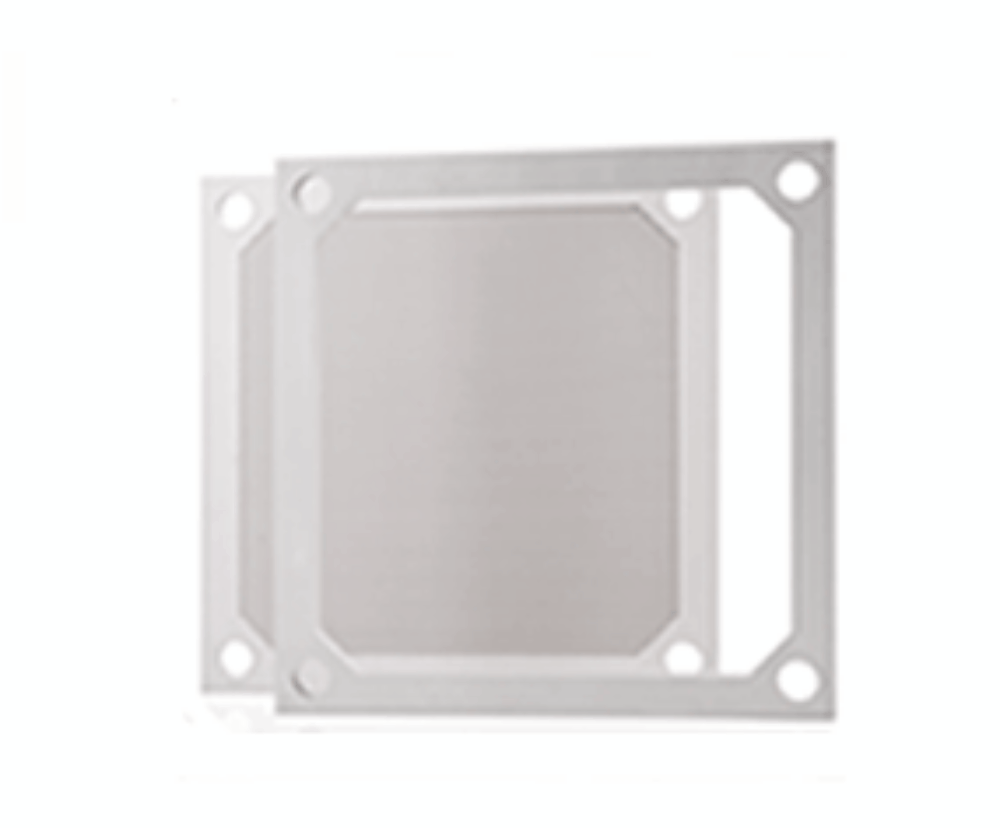
This design has a series of hollow frames and flat surface plates stacked together and supported on rails. Woven cloth material is placed between each frame and plate to collect the slurry material solids and allow liquid to pass through. The stack of alternating frames and plates are held together by mechanical screws or by a hydraulic ram.
With the stack being held tightly together, the slurry material is forced into the frame cavities by some type of pumping actions. The solid material in the slurry continues to build up in the frames as long as the filtrate liquid flows out through the cloths. When no additional slurry can be forced into the frames, the pumping action is stopped. The frames and plates are unclamped then separated one at a time to allow the dewatered cake material to fall out of the frames.
One inherent problem with the plate and frame design is the tendency for the dewatered cake material not to fall out of the frame when opened. Several types of frame shake mechanisms are used to promote cake discharge, but often the operator has to manually dislodge the material from the frames.
Recessed plate
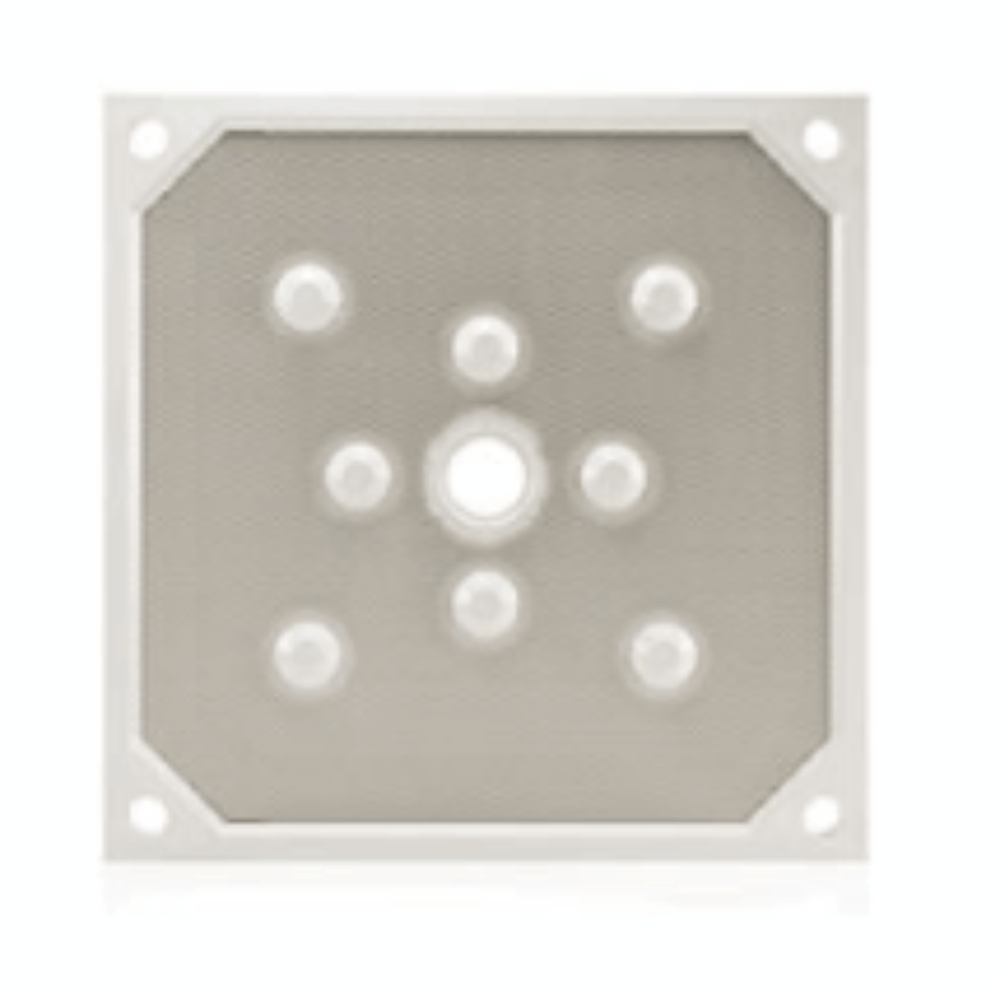
Most modern-day plate Filter Presses employ a “recessed” plate design to replace the frame and flat plates.
When adjacent recessed plates are held together, a chamber space is formed. Filter cloths cover both sides of the recessed plates. Just like a plate and frame press, the slurry is pumped between the clamped stack of recessed plates, where the dewatering occurs. Once the cakes are formed, the feed pump is stopped and the plate stack is unclamped. When the recessed plates are separated, the cakes are much more easily discharged from the plates without being obstructed by a frame.
A more general term used to describe these types of dewatering technologies is Plate Filter Presses. Both recessed plate and plate and frame design Filter Presses are utilized in numerous dewatering applications today. A third common design, membrane plate Filter Presses, uses recessed type plates with flexible plate surfaces that can be expanded into the cake space to compress the formed cake, resulting in additional liquid removal. Membrane plates are only effective when the material being dewatered is compressible.
Myth: The hydraulic cylinder actually squeezes the liquid out of the cakes
One common misconception associated with plate Filter Presses is that the material being dewatered is squeezed between the filter plates by of a hydraulic power unit/cylinder. In reality, the hydraulic cylinder that is used on most modern-day plate Filter Press designs only is used to compress the filter plate stack tightly together and prevent the slurry feed pressure from forcing the plates to separate.
Hydraulic power unit.
Once the plate stack is held tightly together, the slurry is fed into the chamber spaces between the plates. The pumping action and resulting slurry feed pressure are what creates the dewatering action. The pumping action continues until little additional slurry can be forced into the Filter Press. When the pumping action is stopped, the hydraulic cylinder is used to open the plate stack sufficiently so each plate can be separated individually, allowing the cakes to discharge by gravity.
Hydraulic cylinder.
To see how a Filter Press works, click the button below.
Myth: Chemicals are always required in dewatering slurry materials
Chemical additives are most often not required to aid in dewatering when plate Filter Fress technology is used.
Modern-day plate Filter Presses are designed to operate under very high slurry feed pressures from 100 psi (7 Bar) to 225 psi (15 Bar), or more in special applications. These high pumping pressures are possible in the plate Filter Press because filter plates are held tightly together by very high mechanical or hydraulic pressure, typically 2500 psi (175 Bar) to 5000 psi (345 Bar). Because the slurry material is exposed to high feed pressures, much higher dewatering efficiency can be achieved without chemicals aids or additives.
Other common dewatering technologies, such as belt Filter Presses or centrifuges, cannot generate very high slurry dewatering pressure and most often will require chemical additives to achieve reasonable dewatering efficiencies.
Myth: Dewatered filter cakes are dry solid cakes
The amount of liquid that can be removed from a slurry using a plate Filter Press is very dependent on the type and quality of material being dewatered.
Dewatered cakes collect in a bunker beneath the Filter Press.
As the liquid is removed from a slurry, the particles become more tightly packed together and eventually form a “solid” mass that no longer flows easily. Depending the specific material characteristics, the solid mass can form with as much as 50% of the liquid still remaining with the solids.
Filter Presses dewater slurry from a liquid to a more manageable form.
In nearly all cases, some minimum amount (10% to 25%) of liquid will remain in the dewatered filter cakes even when the material is dewatered very efficiently.
Dewatered filter cakes.
Some of the major factors that affect the dewatering characteristics of a slurry include slurry concentration, particle size distribution, shape and origin. Coarse and more irregular shaped material slurries tend to be more easily dewatered, while fine particle slurries can be very challenging to dewater. Flat or uniformed shaped fine particle slurries are more easily packed together, as liquid is removed and can become very difficult to dewater. One of the most difficult slurries to dewater is a very fine particle size, flat shaped clay material.
Myth: All slurry materials have similar dewatering characteristics
Slurries are formed by mixing dry, solid particles with a liquid, very often water.
Solid particles are described by their chemical makeup, particle size distribution, particle shape, specific gravity, abrasiveness, sharpness, hardness and purity. When mixed into a slurry, additional characteristics such as slurry percent solids, specific gravity, viscosity, particle charge and pH are used to describe the solid/liquid mixture. Many, if not all, of these solid material and slurry characteristics can impact how easily or difficult the slurry is dewatered. Because of the many characteristics involved, it is more understandable why no two slurry materials will have the same dewatering characteristics.
The best way to understand dewatering characteristics of a specific slurry is through some type of laboratory or on-site pilot material testing. To obtain the most accurate results, a representative sample slurry must be taken for testing. Sample testing results will typically include slurry percent solids, particle size distribution, slurry pH, slurry specific gravity, filtration rate, final dewatered percent solids, and filtrate water ppm (parts per million) solids. Accurate full-scale equipment sizing and capacity can be accurately predicted once solid material, slurry and dewatering testing is completed.