Introduction
Decanter Centrifuges are used in a variety of applications for the mechanical separation of solids and liquids. They consist of a bowl that rotates at high G-forces, causing the solids to stick to the wall of the bowl in a process called sedimentation. The solids are moved toward the discharge at one end of the machine by a helical conveyor that rotates at a slightly slower speed than the bowl. The liquid is discharged out the other end of the Centrifuge.
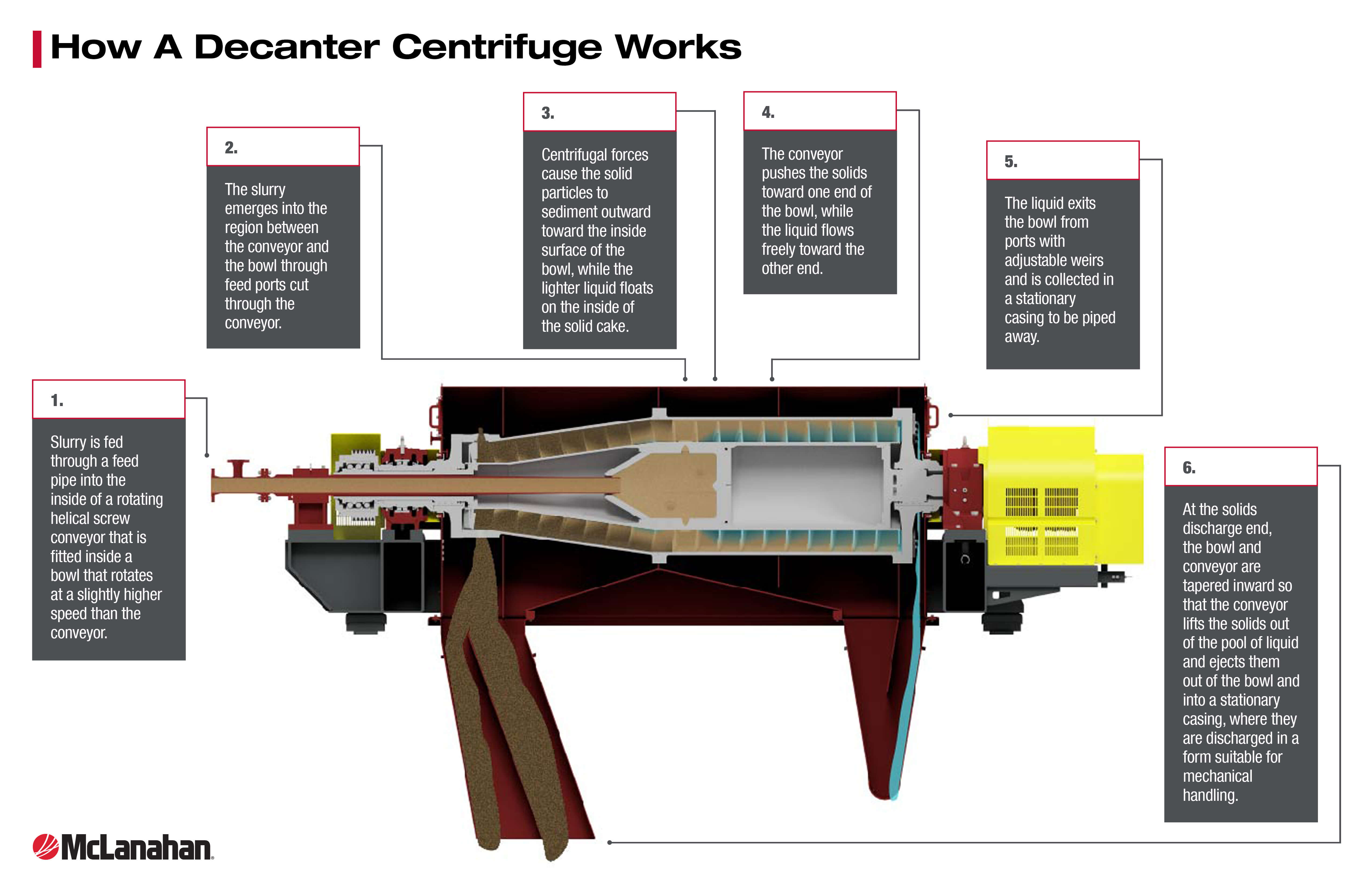
Depending on the goals of the site and whether the solids or the liquid is the more important product, the primary objective of a Decanter Centrifuge can vary between the following functions:
- Drying/Dewatering – a focus on minimizing the amount of liquid in the solids
- Clarification – a focus on minimizing the amount of solids in the liquid
- Washing – a focus on removing soluble contaminants from the solids
- Classification – a focus on allowing fine particles to be removed with the liquid
To ensure the objectives are being met, samples of the solids and liquid should be analyzed to confirm they meet the quality requirements. The performance of the Centrifuge can be improved by adjusting various parts of the process depending on your objectives.
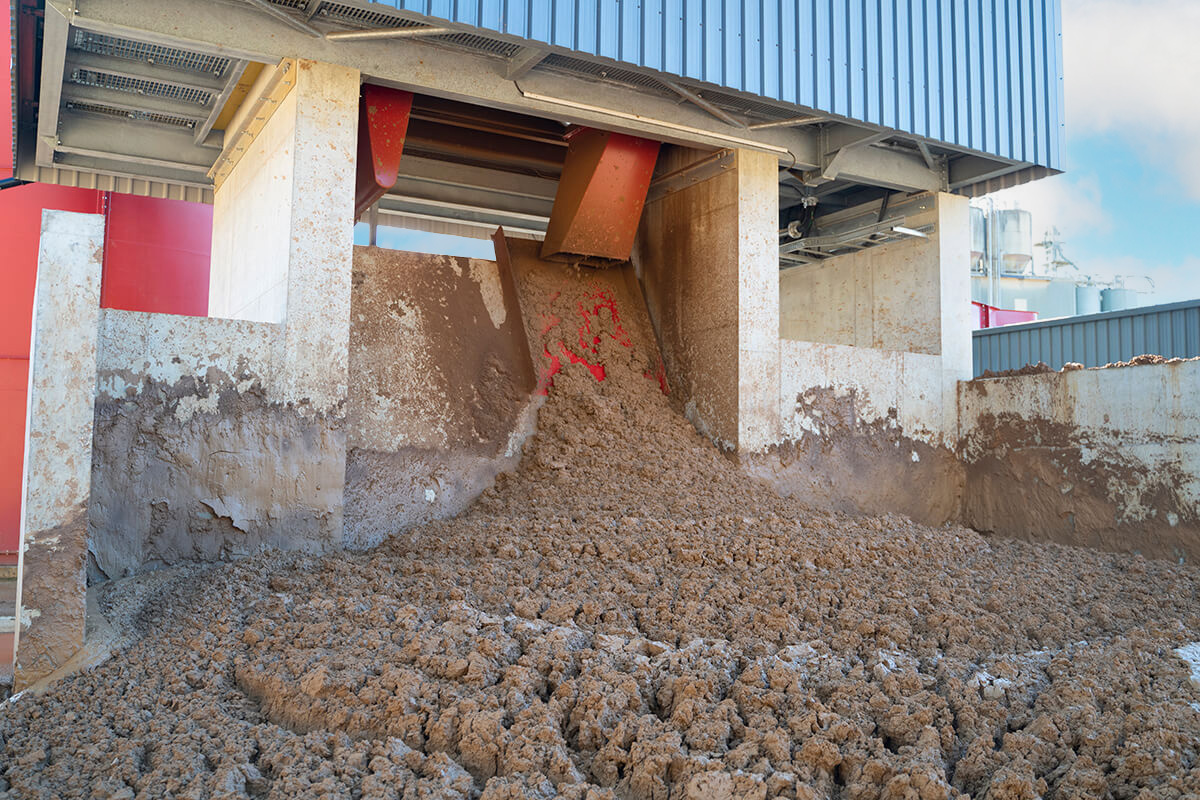
Solids discharged from a Decanter Centrifuge.
Pool depth
The bowl of a Centrifuge is tapered at one end to provide a dry deck area (or beach) that allows the liquid to drain out of the solids as they are conveyed out of the pool toward the discharge.
The depth of the pool can be decreased or increased by adjusting the weir plates over the discharge ports on the liquid end bowl head.
Lowering the weir plates decreases the pool volume by increasing the radius of the discharge ports, decreasing liquid retention time. This also reduces the depth of the pool and increases the length of the beach, allowing more time for the liquid to drain from the solids and creating a drier, more dewatered solids product.
Raising the weir plates increases the pool volume by reducing the radius of the discharge ports, increasing liquid retention time.
This also Increases the pool depth allowing more time for the sedimentation process to take place, resulting in a clearer liquid.
For aggregate tailings applications, deep pools are preferred, as these provide the best centrate clarity at the lowest power consumption.
Depth indicator markings are located beside the discharge port to aid with adjustment. Take care not to adjust the pool depth so much that the liquid clarity or solids dryness becomes unsatisfactory.
Rotational speed
Centrifuges rely on the forces created by the rotation of the bowl for the sedimentation process. Increasing the rotational speed of the bowl increases the G-forces that separate the solids from the liquid, resulting in a drier solids product as well as a clearer liquid product.
The speed of the Centrifuge can be adjusted via the variable speed drive (if applicable) or by changing the size of the drive pulley. Ensure you don’t increase the speed above the recommended maximum setting specified in the operation and maintenance manual. Also, note that depending on the feed material, increasing the speed can actually have the opposite of the intended effect, such as increasing the moisture in certain products, or have no effect at all.
Feeding position
Some Centrifuges have baffles inside the conveyor hub that form separate feed compartments, each with its own discharge port, along the length of the bowl. The feed pipe can be adjusted to feed any of these ports, changing the location where the slurry is introduced into the bowl.
Moving the feed point closer to the liquid end of the bowl reduces disturbances to the cake being formed on the beach and improves the dryness of the solids. Moving the feed point closer to the solids end of the bowl allows improved sedimentation for improved liquid clarity.
Washing
Nozzles fitted on some Centrifuges provide a washing action to remove soluble contaminants and potentially improve solids dryness by allowing liquid still attached to the solids particles to drain.
This washing action should spray liquid onto the solids in the beach area close to the pool. Positioning the nozzles any closer to the solids discharge can negatively affect the drying time and produce wetter solids.
Slurry consistency and feed rate
Especially when working with fine particles sizes (less than 45 microns or 325 mesh), high concentrations of solids in the feed slurry can cause an effect called hindered settling. Hindered settling prevents effective sedimentation, which results in poor liquid clarity. If the feed has a very high concentration of solids, it may need to be diluted.
Conversely, extremely dilute slurries should be thickened in a gravity tank ahead of the Centrifuge, taking care not to overthicken the slurry to the point that hindered settling could occur and compromise the clarity of the liquid.
Liquid clarity can also be improved by reducing the volume of liquid in the slurry, which reduces the velocity and allows the solids more time to sediment.
Chemical treatment
It may be necessary to add flocculant to the slurry to help attract the particles and gather them together to increase their collective weight and improve sedimentation. This allows for better liquid clarity, especially in applications with high solids concentrations in the feed and/or fine particle sizes.
Decanter Centrifuge
Before making any adjustments to a Decanter Centrifuge, it is imperative that you follow all site-specific safety precautions and all safety precautions outlined in the machine manual. You should also test your material to determine what adjustments need to be made. Making simple adjustments to the process, such as to the pool depth, rotational speed, feeding position and the feed slurry, can improve the solids dryness or the liquid clarity, depending on the goals of your site. Just be sure you don’t adjust too much that you compromise the other product while in pursuit of your goals.