Introduction
Preventive maintenance is always cheaper than emergency repairs. The increased cost of urgent parts and process downtime hits an operation in the pocketbook.
Even though it is always good practice to open up a pump for inspection, there are usually external signs of wear and tear because of the harsh environment in which pumps operate. By looking for these signs, an operation can minimize surprise pump failures and treat the issue(s) with planned maintenance. Automation can be used to alert you to some of these warning signs, while visual inspection is required for other warning signs.
Warning Sign No. 1 - Excessive leakage at the gland
Different seals have different levels of leaking at the gland, but there is a normal amount of leaking and there is an excessive amount of leaking. An operator needs to become familiar with what the leakage is supposed to be in order to identify an issue.
A simple adjustment may get everything back in order, or maybe a small repair is needed. Left alone, however, it will become a costly repair that could have been avoided.
Warning Sign No. 2 - Excessive leakage at the liners
In the aggregate world, most slurry pumps have replaceable liners to protect the main body of the pump. Depending on how the liners are worn, the pump can have leakage at the liners. If ignored, the slurry will eventually attack the metal casing of the pump.
Product leakage is a clear sign that the liners may be worn or damaged. Excessive leakage should be addressed immediately with an inspection for damage. In the end, it is a lot cheaper and safer to replace the liners than it is to replace the casing and the liners.
Warning Sign No. 3 - Increased power consumption
A lot of energy is put into a pump in order for it to move the slurry through a pipeline, and over time that adds up. When power consumption increases, it is an indication the pump is working harder to do the same job — or even worse, working harder and delivering less. The added energy cost does not help, but the loss in production can be extremely harmful to the bottom line.
A sudden change in power consumption, whether it is an increase or a decrease, should always be a warning sign that something is wrong. Monitoring a pump’s power usage and setting warning parameters are an important part of keeping a pump in good working order. The best way is to have an automatic trending system, but even just manually recording a data point can improve the situation. A structured monitoring program will put eyes on the equipment and can give an early warning.
Warning Sign No. 4 - Vibration
If a piece of equipment does not have vibration, it generally means it is not operating. Some equipment (such as screens) have a high level of vibration. With a pump, high levels of vibration can be a sign of inefficiency or worn elements. Worn bearings, turbulent flow and inadequate foundations are only a few sources of pump vibration.
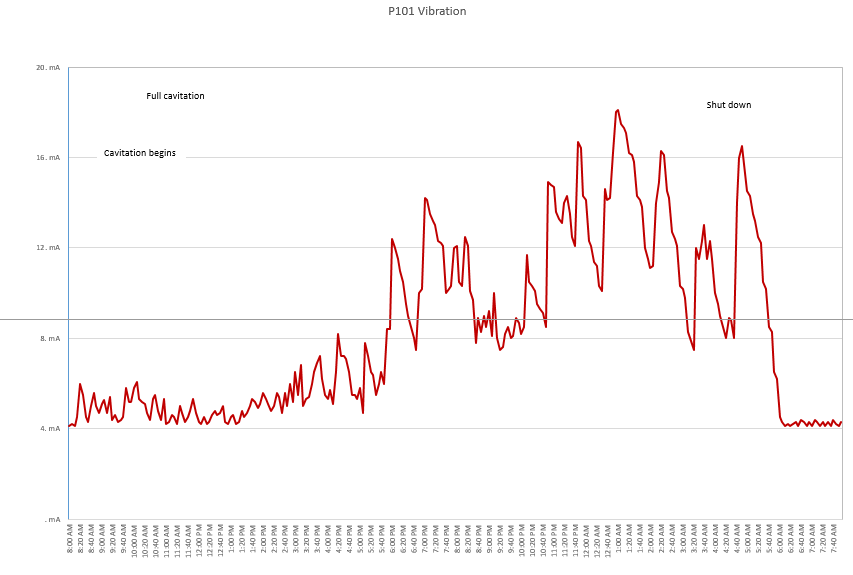
Pumps can be equipped with vibration monitors, which will track the progression of changes or spikes. Much like watching the power consumption, vibration levels will tell a story about the condition of the pump. Even without automated monitors, a good operator paying attention will know something is different.
Warning Sign No. 5 - Bearing condition
The bearing assembly is an important part of any rotating equipment. Worn or damaged bearings can scar the shaft, cause vibration, create high noise levels, generate heat and decrease pumping efficiency.
Because of the noise and vibration, a worn or damaged bearing should be easily spotted by an alert operator. In cases of extended times between visual inspections, a vibration monitor should be put in place. A thermocouple or heat gun can be used to monitor the temperature level to give an early warning.
As any corrosion will rapidly accelerate the rate of wear, it is important to ensure the bearings are always well lubricated and not exposed to moisture.
Warning Sign No. 6 - Noisy pump
Listening to a pump can give you a number of early warnings. One of these warnings alerts you to a different type of wearing caused by cavitation. Cavitation is simply the formation of bubbles or cavities in liquid, developed in areas of relatively low pressure around an impeller. Shockwaves form when these bubbles implode or collapse inside the pump, causing significant damage to the impeller, lining and/or pump housing.
Listen at the suction and discharge end of the pump; cavitation generally sounds like marbles are going through the pump.
Warning Sign No. 7 - Poor belt tension and alignment
The loud, squealing noise of loose belts is annoying, but the real harm comes from the heat generated that eventually causes the belts to fail. The slippage of a loose belt also causes a loss of energy transfer between the motor and the pump.
On the other hand, excessive tension or poor alignment will put a burden on the bearing assembly and the motor mount. Something is going to give, and it is usually the bearing assembly with increased wear.
Excessive tension can also decrease efficiency.
Warning Sign No. 8 - Wearing parts
Certain parts are designed to wear out to act as sacrificial components to protect others. The slurry and operating points have a direct effect on the wear rate. As mentioned above, tracking energy consumption can indicate when the liners are wearing out, but nothing compares to physically examining them during downtimes.
When a process is stable, the liner wear rate should be predictable once a baseline is established. In this case, the passage of time can be a good sign of wear.
Warning Sign No. 9 - Uneven wear on liners
Liners will develop a pattern of wear under stable conditions. Unexpected wear points can direct you to signs of trouble, such as a highly turbulent flow passage, misapplication or sizing of equipment, incorrect operating points or unsuitable materials of construction.
Warning Sign No. 10 - Poor pump performance/flow rate
Monitoring a pump’s flow rate has multiple advantages in relation to how well a process is performing, but it can also give insight into wear components within the pump. A number of issues can reduce the flow rate (such as obstructions), but consistent and long-term decreasing in the flow rate will generally be a reflection of worn liners and impellers.
Every pump has a Best Efficiency Point (BEP) on its operation curve. Knowing where your pump is operating on the curve in comparison to the BEP can give you a heads-up to potential problems. When a pump slips in its performance, as shown by the flow rate, it moves away from its BEP and increases wear and tear on the pump.
Dependable flow meters can be a significant investment, but they can provide valuable insight for the process and pump’s condition.
Warning Sign No. 11 - Repeated failures
A pump will break down sooner or later, that is a given. When the same pump has repeated failures over a short period time, it is an indication something is substantially wrong. Whether it is the wrong pump for the duty, poor quality replacement parts or an improper repair procedure, it is a sign the overall pump installation needs to be reviewed.
Tracking and documenting repairs can help pinpoint the issue and allow a long-term fix to follow. In many cases, a repurposed pump can be undersized or oversized for the application. Both of those situations can cause problems, as shown by the “Effects of operating a pump off its BEP” chart above.
It is a costly and frustrating lesson to learn, but when a pump fails multiple times in a short period of time, it is a good time to bring in the manufacturer for a review.
Warning Sign No. 12 - Line pressure
Without a flow meter, there is another method to monitor the flow rate indirectly. A constant flow rate in a constant pipeline volume will produce a constant line pressure. A change in line pressure may not tell you exactly what has changed, but it will tell you something has changed. When it comes to pumping slurry, unexpected changes are bad news.
Warning Sign No. 13 - Air in discharge
Anyone who has been around pumps knows that air and centrifugal pumps are not friends. Air in the discharge may mean air went through the pump. Even if you do not hear it at the pump, cavitation may be occurring.
Warning Sign No. 14 - Sump level
Dramatic swings in sump level can indicate a number of issues with the pump itself, but it can also cause problems to the pump. Since a centrifugal pump requires a head to operate, changes in the head (as shown by the sump level) can point to future and current problems.
Warning Sign No. 15 - Poor downstream equipment performance
While a pump is only providing material handling, the downstream equipment usually requires that the slurry fall within specific parameters. In the case of a Hydrocyclone, changes in the flow rate will change the cutpoint of the cyclone. Air in the line will disrupt a Separator’s ability to form a syphon.
When downstream equipment is not functioning properly, the overall performance of the process can be severally harmed. A pump is an important part of any wet process system, and when the pump is not performing, the signs show up everywhere downstream.
The pump will tell you when it is in trouble. You can listen for the whisper and have plenty of time to address the issue, or hear it scream in the middle of the night.