Introduction
Fine Material Screw Washers, also called sand screws or screw washers, are simple and well-known equipment for washing, classifying and dewatering sand. They have been a staple in the industry for many years, and for good reason. Screw washers can process high volumes of material and adapt to fluctuations in the feed with less power consumption compared to other types of sand washing equipment.
Screw washers can also last a long time, with many operating for decades in the field. If you’re having issues with your screw washer performance, it is most likely caused by a lack of water or too much water, or the screw wasn’t sized right in the first place. Sometimes, producers can push these machines past their limits, asking them to do more than the design parameters intended. In all these instances, the producer may experience performance issues or inefficiency that can have them wondering if there is a better sand washing option.
If you find your sand screw isn’t performing as well as you’d like, you don’t have to start looking for a new sand plant just yet. You can optimize your screw for several different functions to make it work best for you.
For fines retention
Screw washers are used to separate undesirable fines from product-sized sand. Sometimes, however, product-sized fines may overflow with the wastewater. To retain these “good” fines, you can make slight adjustments to your process or to the screw itself.
Adjust overflow weirs
Fine Material Screw Washers are designed with adjustable overflow weirs at the sides and back of the washer box at the feed end of the machine. These weirs can be raised or lowered to increase or decrease fines retention. Raising the weirs allows less material to overflow to waste and more fine material to be retained, making a finer cut. Lowering the weirs allows more material to overflow to waste, making a coarser cut.
For optimum fines retention, the weirs should be set level.
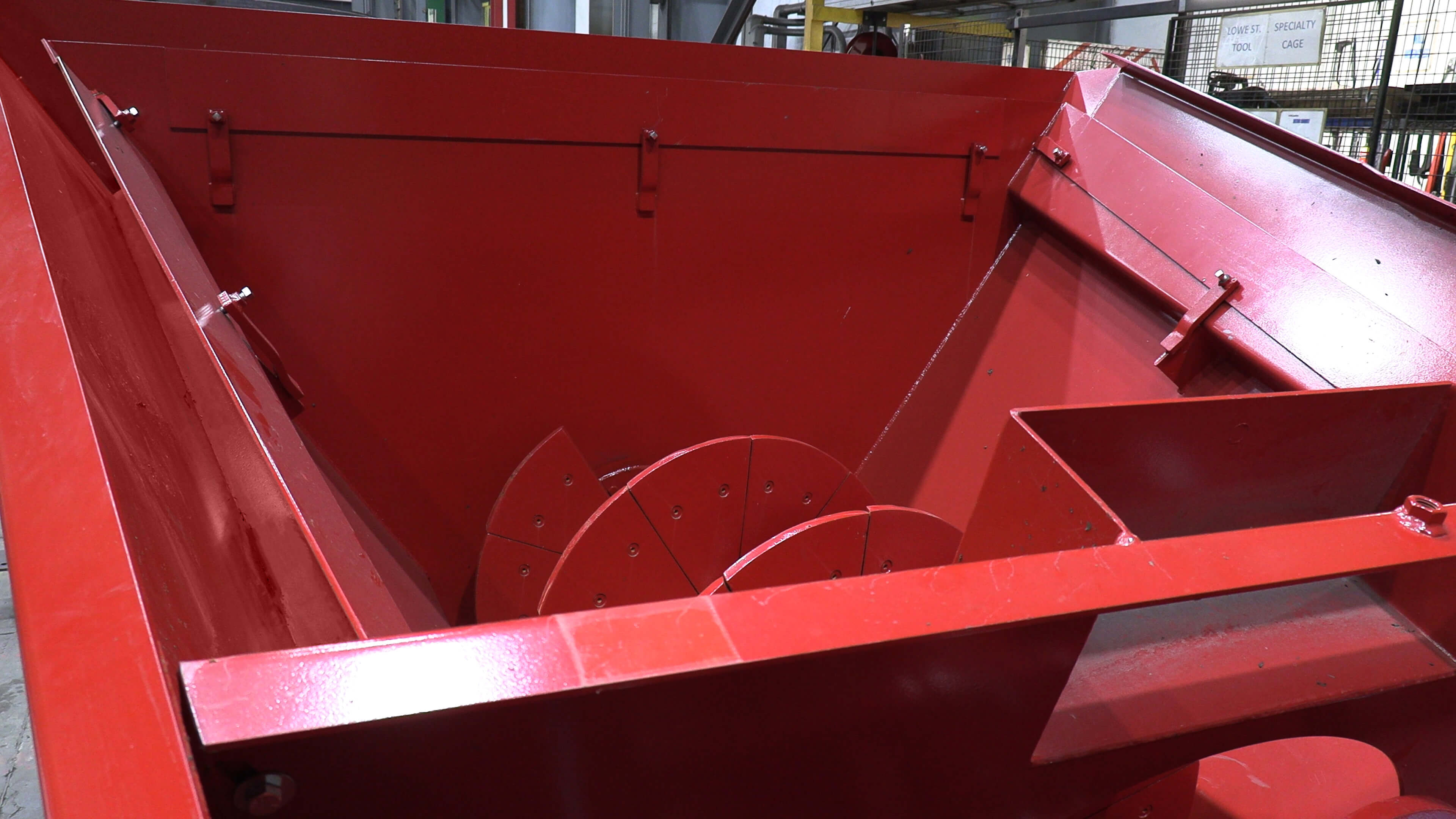
Adjust rising current classification
Fine Material Screw Washers can be equipped with a rising current classifier to help remove unwanted fines. The mechanism injects a rising current of water beneath the pool area to separate the fines and keep them in suspension so that they overflow with the wastewater.
If product-sized fines are overflowing to waste, reduce the flow of water to the rising current classifier or shut it off completely.
Correct improper slurry feed
If increased fines retention is desired, don’t forget to check your feed stream, including the makeup of the feed and how the screw is being fed.
In regard to the makeup of the feed, beware of overloading the screw, either with too much water or with too many feed streams. Screws are sized for both water and solids in the feed, and each size machine requires a specific water volume to make a desired cut. If the feed stream exceeds the amount of overflow for the desired cut, the excess water may carry product-sized fines with it to waste.
Check the water and material balance to ensure the overflow matches the desired retention goal This may require removing a dilute stream to be treated in a different manner in order to optimize screw performance.
In regard to how the screw is fed, for optimal settling of product-sized fines, the pool area behind the baffle plate should be as calm as possible. Too much turbulence in the pool area can prohibit the good fines from settling.
To minimize turbulence and maximize fine sand retention, ensure the sand-slurry feed is directed to the discharge side of the baffle plate. The baffle plate helps to separate the washing area from the feed area to keep the pool area calm.
Adjust screw speed
Although the screw shaft speed is often set by the manufacturer to achieve the goals of the application, it can be adjusted to retain or remove fine sand. The faster the screw speed, the harder it is to convey fine sand. The fine sand will slide off the screw flights back into the washer box, which can cause the fines to build up in the washer box.
For finer sand applications, the screw speed may need to be reduced to ensure the fines stay on the screw flights to be conveyed toward the discharge. Keep in mind, however, that a reduction in screw speed will also reduce overall capacity of the unit.
For fines recovery
If you’ve optimized your screw for fines retention and are still seeing a loss of product-sized fines to waste, don’t fret. You can recover those fines without having to replace your screw.
Add a Scavenger System
To recover product-sized fines being sent to waste, consider adding a Scavenger System. Scavenger Systems consist of a Sump, Pump and Separator™, which is installed over the discharge end of the screw. Overflow from the screw washer is directed to the Sump instead of to waste. From there, it is pumped up to the Separator™. The Separator™ recovers the product-sized fines and discharges them as partially dewatered sand onto the dry deck area of the screw.
Another benefit of recovering product-sized fines with a Scavenger System is a reduction in the amount of material reporting to the settling pond. This can have the added advantage of reducing pond cleanout frequency and maintenance.
Just be sure the addition of the product-sized fines will not throw your final product out of spec.
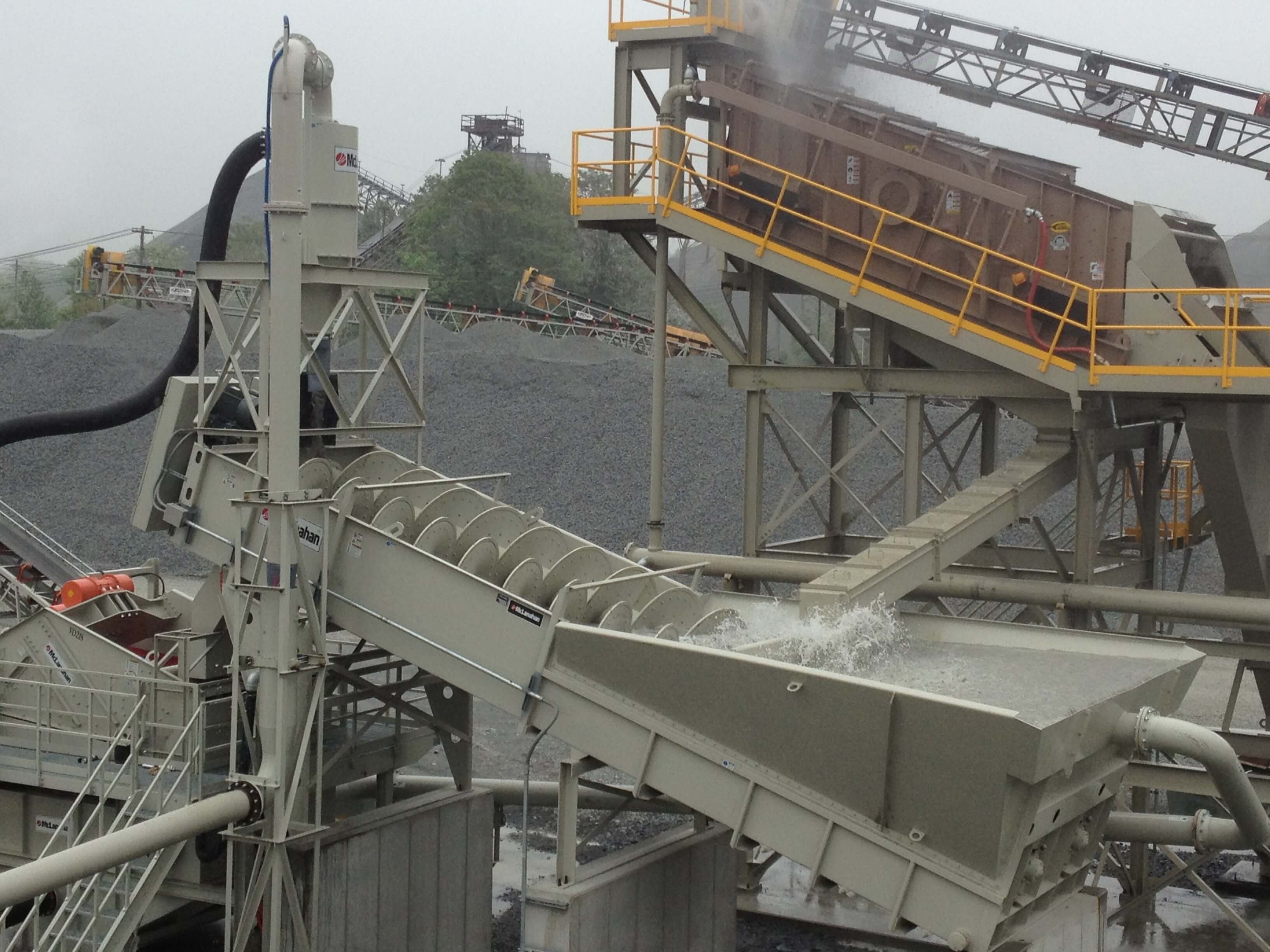
For a drier product
Fine Material Screw Washers offer some level of product dewatering, discharging sand with a moisture content of around 20% depending on the application. The sand is stackable and conveyable; however, the stockpile will often have to sit for a while so that excess water can leach out before the product can be sold.
If you want a drier product from your screw washer, you have a few options.
Correct washback or flushing water
Although it may sound counter-intuitive, adding washback or flushing water in the dry deck area of the screw can actually improve product dryness.
Here’s how.
As sand is conveyed up the inclined dry deck area toward discharge, excess water and fines drain from the sand. In a single shaft setup, the sand is conveyed up one side of the dry deck area and the water drains on the other side. In a dual shaft setup, the sand is conveyed up the middle of the dry deck area and the water drains on the sides. Washback or flushing water is typically injected via nozzles on the drainage side to direct excess water and fines back to the pool area.
Without washback water or with the incorrect amount of washback water, fines can build up on the dry deck, limiting the amount of dewatering that can take place and discharging a wetter product.
To improve product dryness, ensure the correct amount of washback water to allow for a clear channel for the water to drain. A rule of thumb to remember is that the washback water should be enough that you can see the metal of the curved dewatering plate lining the dry deck area.
Add a dewatering screen
Dewatering Screens produce a drip-free product that is stackable, conveyable and ready for immediate sale. They can be installed directly under the discharge end of the screw to accept the partially dewatered material and produce a drier product than a screw alone. This reduces the amount of water discharging with the sand and the amount of time the stockpile will have to dewater before it can be sold. In some cases, sand discharged from a Dewatering Screen can be sold immediately.
Not only does the addition of a Dewatering Screen improve stockpile maintenance, but it also improves overall site housekeeping. Less water in the product means less mess underneath conveyors. It also reduces belt cleaning maintenance associated with wetter sands, which can cling to and build up on the conveyor.
For improved efficiency
If you have excess fines or water in your feed, you can improve the efficiency of your screw by pre-washing the material.
Feed with a Separator™
Separators™ can be used to feed Fine Material Screw Washers with the added benefit of removing minus 200 mesh material ahead of time, providing a pre-washing of the material before it enters the screw. This ensures a nice clean feed to the screw and allows it to operate more efficiently.
Similarly, Separators™ can also be used to reduce water from dilute feed streams. As aforementioned, screw washers require a set amount of water to make a desired cut. If the feed stream is too dilute and exceeds the amount of water needed for the desired cut, a Separator™ can scalp out some of the water ahead of the screw to improve efficiency. This also saves you from having to upgrade to a larger screw to handle the excess water.
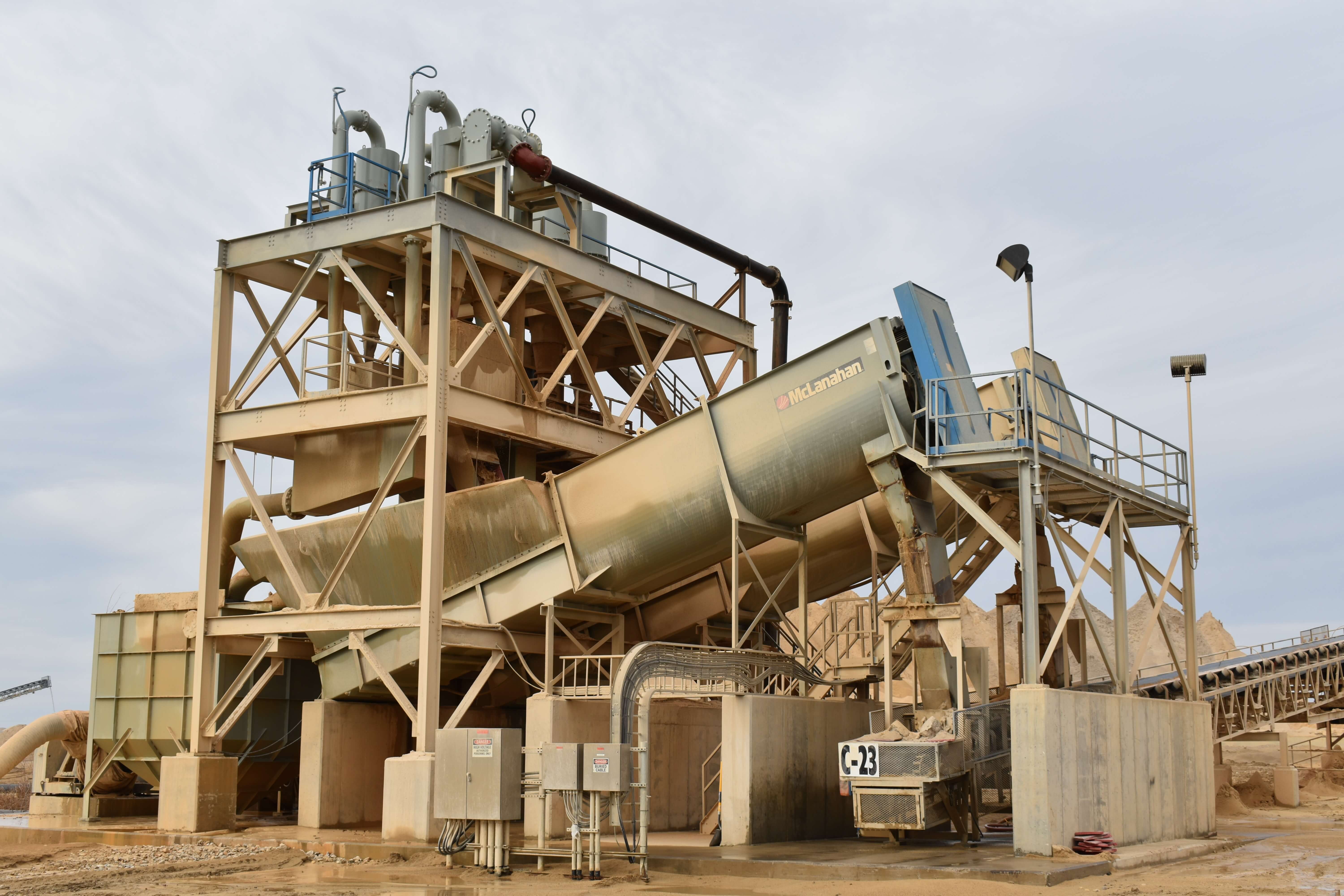
Fine Material Screw Washers are still a great choice for washing, classifying and dewatering sand. To optimize your screw for your application, consider adjustments to the overflow weirs, rising current classifier, slurry feed and screw speed to retain product-sized fines. To recover fines lost to waste, consider adding a Separator™ to process the overflow, or consider feeding the screw with a Separator™ to improve efficiency. For a drier product, check the washback water or consider adding a Dewatering Screen to put the finishing touches on partially dewatered sand discharged from a screw.
With these adjustments to the screw and/or process, or with the addition of lower-capital-cost processing equipment, you can ensure your screw is operating optimally for your application.