Manual sample collection methods
Let’s take a look at a few of the more common methods of manual sampling.
Stopped belt sampling
Of the many manual sample collection methods available, the stopped belt sample is the most accurate – though probably the least efficient. Stopped belt sampling allows for the complete removal of all material particles within a region on the conveyor belt, which is physically bounded by a set of dividers.
Unfortunately, this also requires that the conveyor belt be stopped (with proper lockout/tagout procedures followed) while each increment is collected – a situation that is unlikely to be very popular with operations personnel or plant management.
A stopped belt sample is, however, a good reference for discussing what an ideal sample increment should be, particularly since potential dynamic problems are not present, as neither the divider (cutter) nor conveyor belt is moving while the sample increment is removed. In fact, most bias testing involves some variation of comparing samples collected under normal operating conditions with stopped belt reference samples.
There are several key benefits to collecting samples by the stopped belt method.
1. Safety
The first item, as always, is safety. Stopped belt sampling is a relatively safe method to collect manual samples, as no moving material or operating equipment are involved.
Obviously, there can be some safety concerns that arise from the specific location from which the sample is to be removed, but this will vary from facility to facility.
2. Equal probability
Second, the sample is equiprobable, which means all material passes the point from which the sample is removed and could be included in a sample increment depending on when and where exactly the belt comes to a stop.
3. Delimitation
The next item is that the sample increment is properly delimited. This means that the boundaries of what will be the sample increment are clearly defined – no outside material can enter and no material inside can escape. Only material within the predetermined cutter width will be collected.
This is important since the increment mass of material on the belt must be proportional to the flow on the conveyor belt at the time the increment is collected. Variations in sample increment mass lead to inconsistencies in final save sample, which lead to biased sample analysis.
4. Constant cutter width
The next item is that the stopped belt divider can be maintained at a constant width across the whole cross section of material on the conveyor belt. Similar to delimitation, the constant cutter width is critical to maintaining a consistent and proportional increment mass.
5. A full depth sample across the full cross section
In addition to the increment mass concerns, an increment that collects the full depth of material across the full width of the cross section is important because material is not likely to be consistent throughout the whole cross section. This is especially true with belt conveyors since material tends to segregate on belt conveyors.
If material is not collected at full depth, material that is at the bottom of the conveyor cross section (fines) will not be properly represented in the final sample. If material is not evenly loaded across the conveyor belt, material from one side of the belt or the other will not be properly represented in the final sample.
With stopped belt sampling, it is relatively easy to collect all the particles contained within the dividers. It is also relatively easy to verify that all the particles have been collected. Since the belt is stopped, enough time is available to successfully collect the sample.
Stockpile sampling
Perhaps the most common manual sampling method for aggregates is stockpile sampling. There are different approaches to collecting a sample in this fashion, but all methods exhibit the same issues to some degree or another.
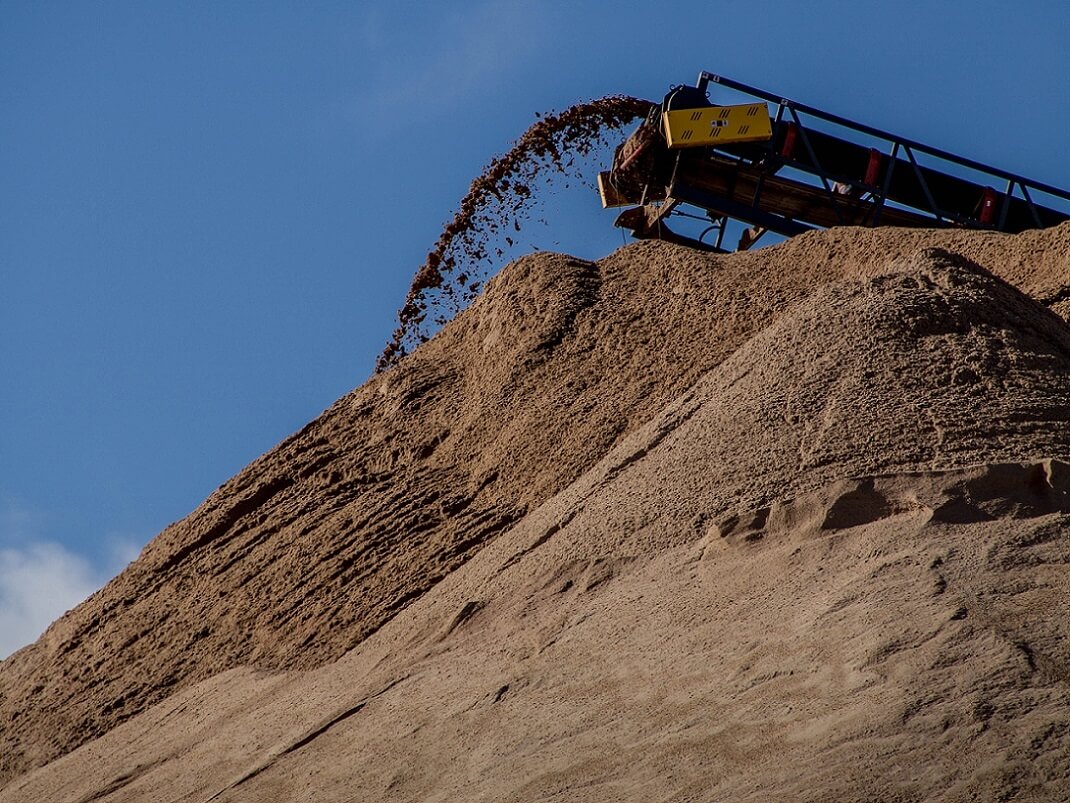
Stockpile sampling methods involve collecting material directly from the product pile.
1. Safety issues
Again, the first issue is safety. Sampling from stockpile requires that personnel be on, or at least in very close proximity to, a stockpile. Since stockpiles can be somewhat unstable and unpredictable – especially while material is being removed – it is likely best that personnel are kept away.
Some methods will keep operators at a safer distance by employing mobile equipment to complete the preliminary material removal from a stockpile. While this does keep personnel safer, sampling in this way still does not address some other problems with the sample collected.
2. No equal probability
All particles within the stockpile will not have an equal chance of being selected as part of the sample. Since material entering the stockpile is usually segregated on the conveyor belt feeding a stockpile, material is not distributed into the stockpile in a uniform way.
Furthermore, once material enters the stockpile, it does not settle in a uniform way, amplifying the issue of non-uniform material distribution within the stockpile. If material is not uniformly distributed, and all particles within the stockpile do not have the same chance of being collected, it is very likely that the accuracy of any samples collected will be reduced. The sample will not closely represent the material present in the stockpile.
3. Not properly delimited
Stockpile samples are also unlikely to be properly delimited (it is not possible for the stockpile as a whole). It is very difficult to define the physical boundaries inside of which sample will be removed if only a portion of the stockpile is considered. Again, considering that only a small portion of the stockpile is sampled, it is likely possible to collect a sample of constant width, but this is not possible for the stockpile as a whole.
4. Not possible to sample across full width of depth
It is not possible to collect samples from the full cross section or full depth of the stockpile, which means that changes in the makeup of the stockpile will not be represented in the sample that is analyzed. The sample collected is a subjectively located, partial section sample that is only truly representative of the area from which the sample was collected.Therefore, it is not likely to accurately represent the stockpile as a whole unless material in the stockpile is very uniformly distributed throughout the stockpile.
Transfer point sampling
Aggregate samples are also commonly collected at a transfer point, such as from a falling material stream discharging from one conveyor onto another conveyor. Oftentimes, this is done manually using a small container or handheld cutter/collection device.
1. Safer than stockpile sampling
Transfer point sampling may be arguably safer than requiring personnel to work on or alongside a stockpile, but it still requires personnel to be exposed to operating equipment and falling material flows (not to mention manually inserting a device into the falling material flow).
As a side note, it is probably worth mentioning that automated equipment can be used to safely collect correct samples from a falling material stream.
2. Equal probability
This method of sample collection is at least equiprobable, as all material making up the lot of material to be represented will flow past the collection point.
3. Possible delimitation
Delimitation is likely a concern depending on the type of sample collection implement used, though it should be possible to get correctly defined boundaries for the sample increment if the implement is designed properly.
4. Cutter must move at a constant speed
The major issues with transfer point sampling, however, are a function of implement design and how the implement actually interacts with the falling material stream. Since this method involves a moving cutter, it becomes important to ensure that the cutter moves through the material flow at a constant speed to ensure calculable and consistent sample increments. If the sampling device does not move through the material flow at a constant speed each time, more or less material can be collected with each increment. This results in a disproportionate amount of sample being collected with each increment, which can cause issues in the final analysis of sample collected.
5. Difficult to sample a full cross section
It can also be very difficult to manually collect a full cross section of material from a falling material stream, as the sampling implement should be sized large enough to contain the full amount of material expected in a full cross sectional increment. This amount of material can be difficult to handle manually while also trying to maneuver the sampling device through the material flow.
The requirement of collecting sample to the full depth of the material cross section is less of an issue here so long as the sampling implement is large enough to contain the entire increment and deep enough to prevent material from rebounding back out of the sampling device while the increment is collected.
Automatic sampling with Cross Belt Samplers
The question becomes then, how to collect a correct, representative and consistent sample with minimal impact on plant operations?
It seems that the ideal situation would be to combine the sample integrity associated with a stopped belt sample with a more efficient means of sample collection, or an automated stopped belt cut, so to speak. This is exactly the sort of situation that lends itself well to the use of a Cross Belt Sampler.
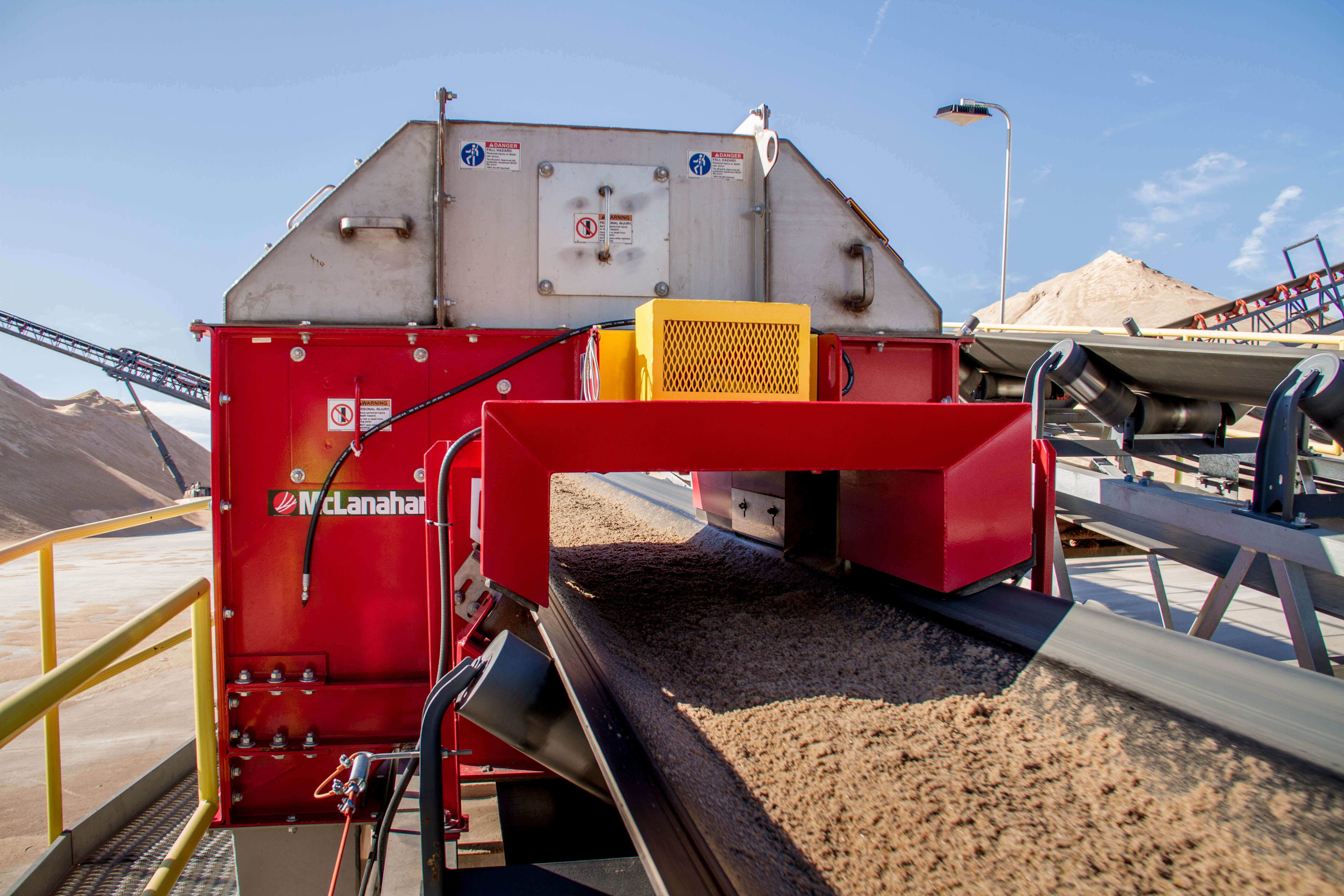
A McLanahan Cross Belt Sampler automatically collects samples of concrete sand at this site in Oklahoma to ensure quality.
A Cross Belt Sampler is a safe, cost-effective and easily implemented solution that will collect representative samples. It is installed on existing conveyor structure (around the conveyor belt). A sample is collected when a rotating cutter assembly travels through a 360 degree rotation, passing through the moving material stream on a conveyor belt and depositing the sample collected into the discharge chute of the sampler as the rotating cutter assembly stops.
1. Safety
This means of sample collection is safe, as no operators are exposed to the moving conveyor or material flow.
2. Equal probability
It is also equiprobable, as all material must pass beneath the sampler on the conveyor belt in question and therefore has the possibility of being collected as part of the sample.
3. Proper delimitation
The sample cutter properly delimits the increment to be collected, as the increment is fully bounded by the conveyor belt below and the cutter side plates at the beginning and end. A properly designed cutter will have parallel side plates (constant width throughout) that can withstand the abuse inherent with this type of application, and can collect a full cross section of material at the full depth of the material.
4. Collect fine material with Cut Zone System
It is also worth noting that a concern that is commonly raised with Cross Belt Samplers is that fine material located at the bottom of the material cross section may not be collected with this type of sampler. While it is true that this is the most difficult material for a cross belt type sampler to collect, it is also true that a Cross Belt Sampler can collect this material. The successful collection of fine material is dependent upon proper design and adjustment, as well as the incorporation of a conveyor belt contouring system, such as the McLanahan Cut Zone System.
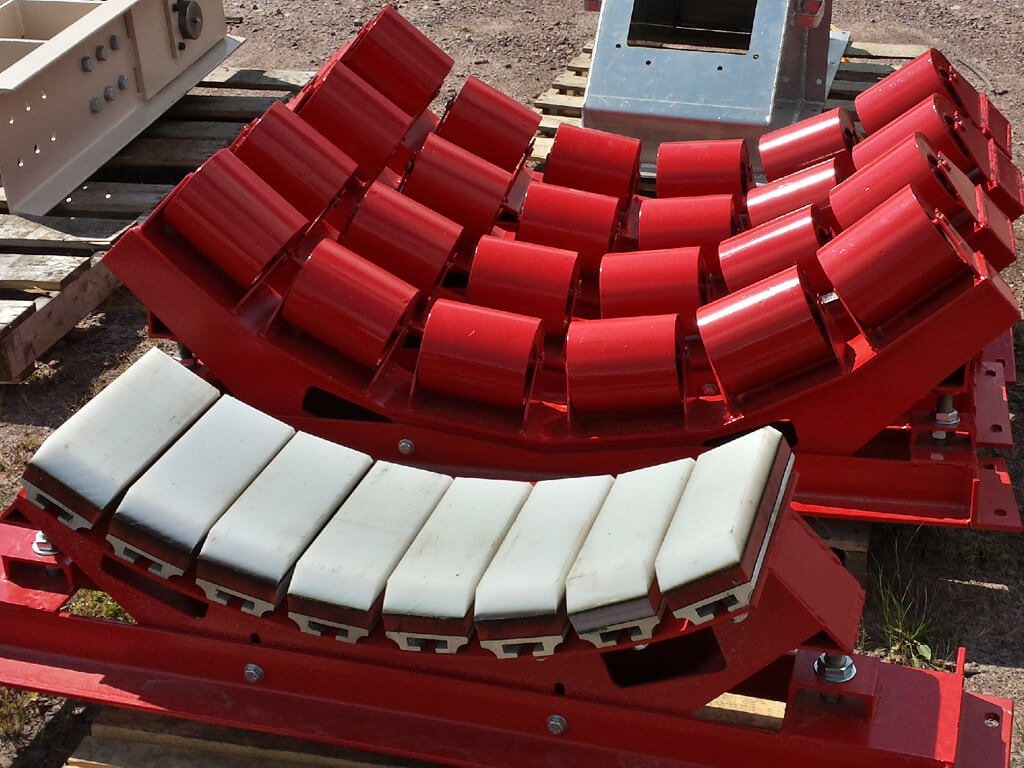
McLanahan Cut Zone System for Cross Belt Samplers.
A Cut Zone System conforms the conveyor belt to the radius of the sample cutter, which allows for the close adjustment necessary to collect smaller particle sizes. The Cut Zone, along with proper adjustment, will allow for successful implementation of Cross Belt Samplers.
Cutter motion
In Cross Belt Sampler applications, it is important to consider the profile of motion of the cutter as well as the motion of the cutter with respect to the conveyor belt since both the cutter and the conveyor belt are moving. A sample cutter moves through four phases of motion while an increment is collected.
1. Acceleration
The first phase is acceleration. With acceleration, the key consideration is to be certain that the cutter assembly can accelerate to its full rotational speed before the cutter enters the moving material stream being sampled.
2. Steady state motion
The second phase is steady state motion. Generally, acceleration occurs quickly enough that a period of time exists where the cutter assembly is rotating at full speed before entering the moving material flow.
3. Material collection
Third, is the actual collection of material. It is important during this phase of cutter motion that the cutter assembly maintains its full rotational speed through the entire period of time that the cutter is interacting with the material flow. This is to ensure a correct, accurate and repeatable sample increment. Undersized samplers with smaller drive units will often slow down while an increment is collected. While this allows for a more inexpensive machine, it also compromises the integrity of the sample collected.
4. Deceleration
The last phase of cutter assembly motion is deceleration. Deceleration must take place very quickly once the cutter has left the moving material flow to discharge the sample material from the cutter while keeping the cutter stopped in a position where any sample material that is not immediately flung from the cutter can continue to slide down and out of the cutter in the parked position.
The Cross Belt Sampler collects a product sample without stopping the conveyor belt.
Cutter speed
The speed of the cutter assembly with respect to the conveyor belt speed is also important. The tip speed of the cutter is used for comparison purposes with belt speed, but in general, the cutter speed should always be faster than the belt speed. How much faster usually varies by application, but a minimum value is often expressed as a cutter velocity that is at least 1.5 times the conveyor belt velocity. This minimum value is commonly used in a number of industries, though in actuality, it may be advantageous to exceed this minimum value, and faster than minimum speeds are often encountered.
Remote operation
An automated means of sample collection also offers the benefits of remote and/or automatic operation. It also provides quality control personnel with a better means of process monitoring, as it allows for the inspection of material as it is produced before it reaches the stockpile and becomes intermingled with other material.
Cost savings
Sampling equipment is not typically regarded as production equipment – equipment that is directly tied to producing a finished product – and thereby not regarded as equipment that will generate a profit. While that may be technically true, the costs of not sampling or not sampling correctly can have a significant impact on the bottom line of a production facility. These costs may not be immediately visible or easily quantified, but they do exist in the savings that can be realized by increased safety for sampling personnel, tighter quality control of the end products, improved ability to assign an accurate value to product sold and increased efficiency in the plant.
The case for Cross Belt Samplers
With an ever-increasing focus on product quality and plant efficiency, it is important to implement a quality control program that provides highly reliable data on plant performance and product specification while allowing for a high plant availability and efficiency. In aggregates sampling applications, a Cross Belt Sampler allows quality control personnel and plant management to meet this important compromise.