Blade Mills
Blade Mills, also known as Aggregate Conditioners, scour, abrade and break down water-soluble silts and deleterious clays from contaminated ores, coarse rock or sand feeds.
Applications
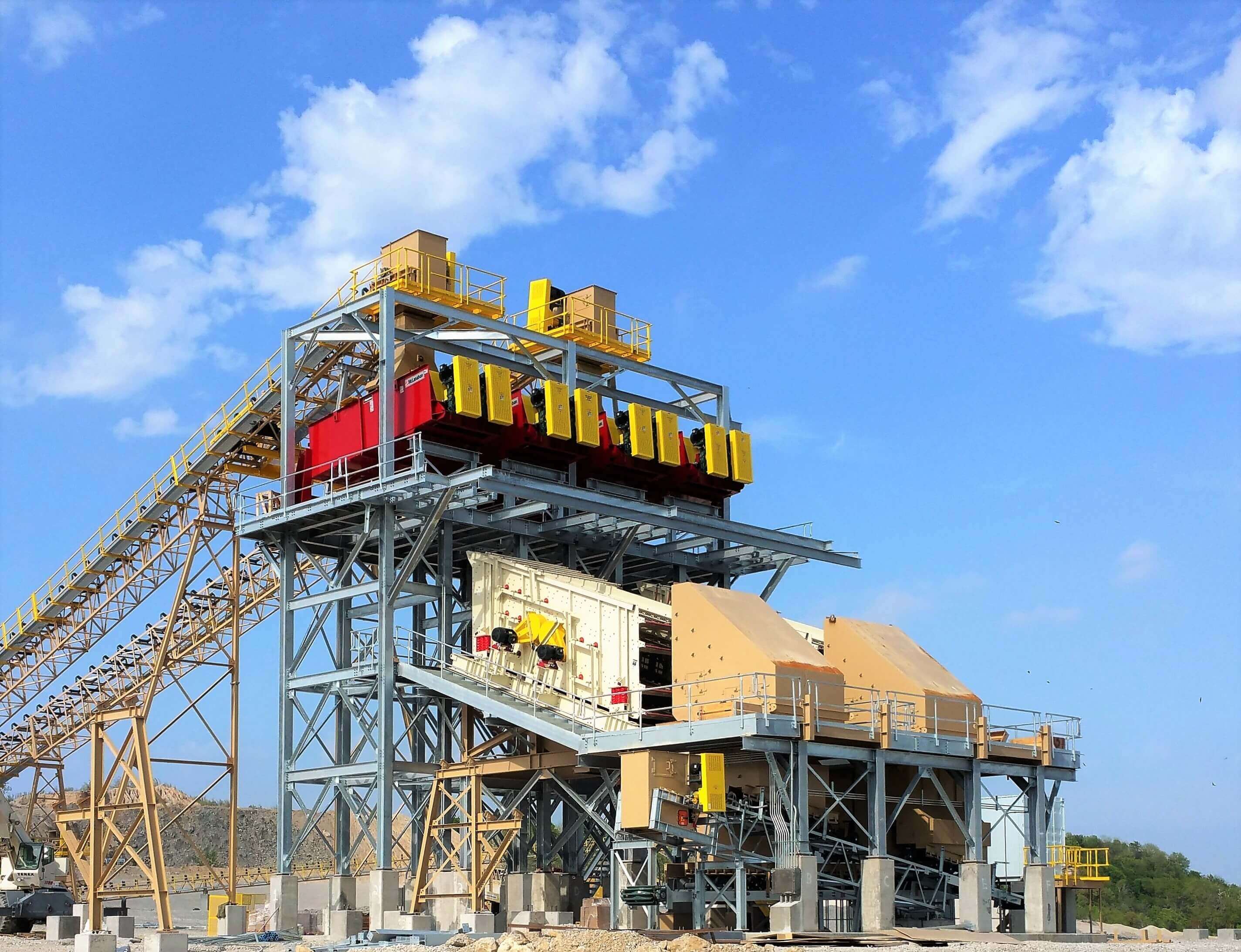
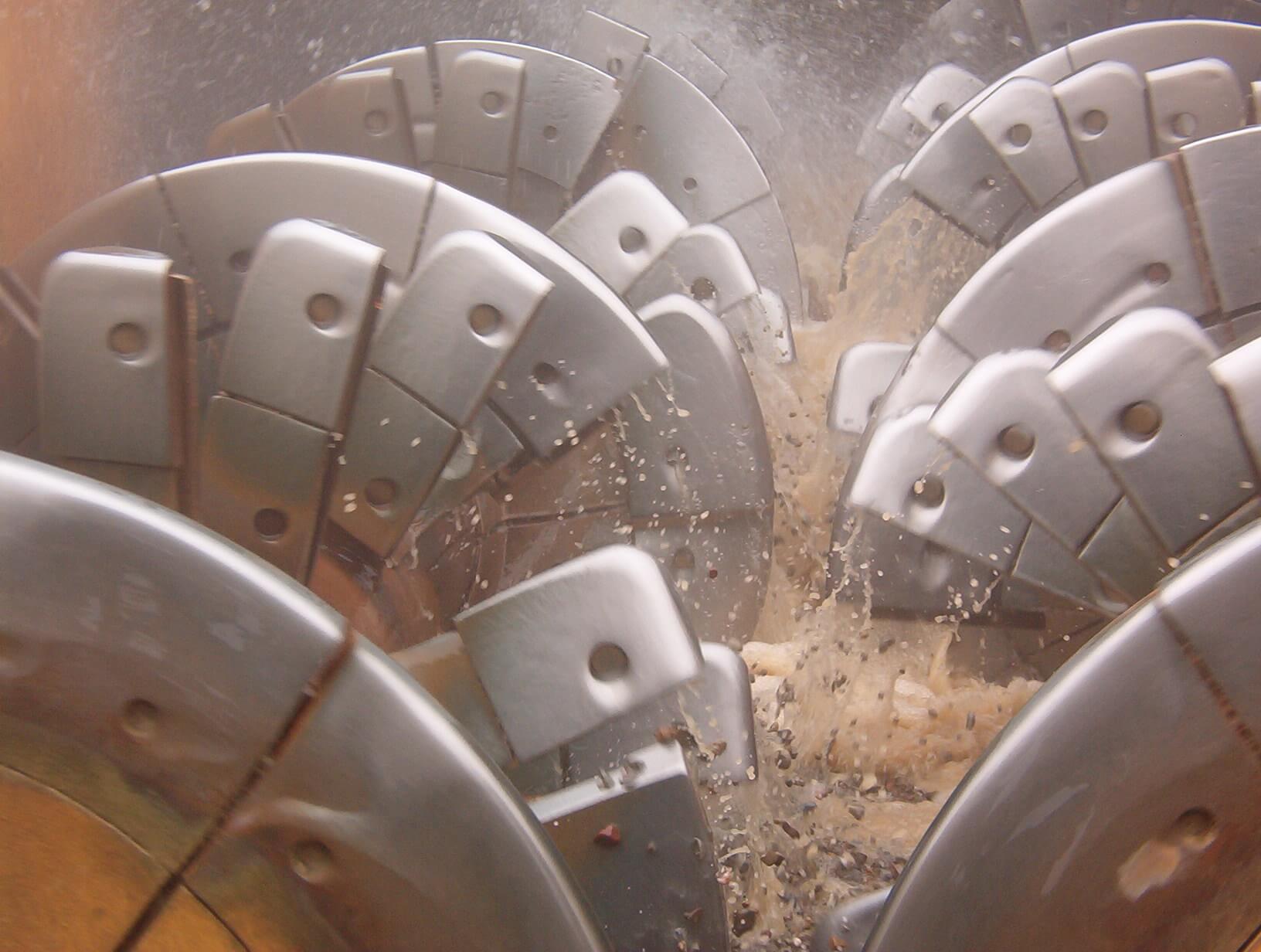
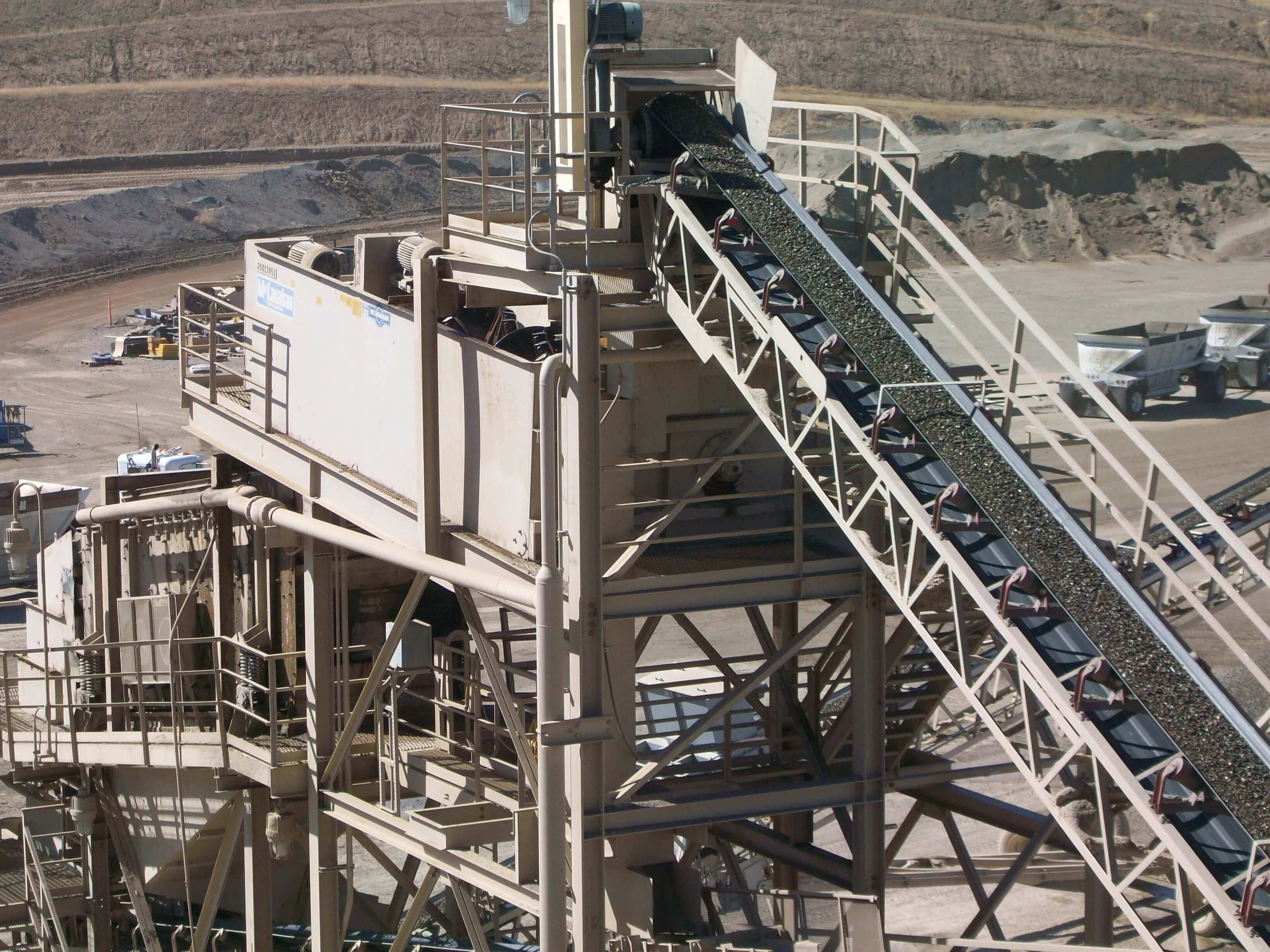
Blade Mills, also known as Aggregate Conditioners, scour, abrade and break down water-soluble silts and deleterious clays from contaminated ores, coarse rock or sand feeds.
Applications
Jump To:
Blade Mills scour, abrade and break down deleterious material using a combination of paddles and flights arranged in alternating format the entire length of the shaft to scour, abrade and break down deleterious material. The shafts can have different configurations, but mainly feature alternating flights and paddles.
Blade Mills sit on a slope of 0 to 5 degrees and have higher capacities compared to Coarse Material Screw Washers of the same size. This is primarily due to the lower machine operating slope of the Blade Mill. Generally, the amount of water needed for a Blade Mill is an additional third of the weight of material being processed.
A Blade Mill is used where the material needs to be worked and wetted before it enters other wet processing equipment, such as a Vibrating Screen, Fine Material Screw Washer or Sand Classifying Tank. They are most often placed ahead of wash screens to improve screening efficiencies or in front of other wash equipment to improve the Sand Equivalency (SE).
Despite being very similar in appearance to Coarse Material Screw Washers, Blade Mills process material differently. For instance, all material that enters the box, must exit through the discharge opening as there is no overflow weir. Without an overflow weir, material must be discharged into another piece of process equipment and cannot be put on a conveyor belt.
Blade Mills are predominantly used for washing contaminated construction aggregate that needs to be scrubbed due to soundness or sand equivalency requirements, as well as many non-aggregate hard ores that contain water soluble clays and silts.
McLanahan Blade Mills are available in single and double shaft designs depending on capacity requirements. The smallest 20” (508 mm) diameter single shaft Blade Mill can be used for capacities of 20 to 40 tph, while the larger 54” (1370 mm) diameter twin shafted machines can be used at capacities ranging from 600 to 1,000 tph. They sit at a slope of zero to five degrees and can achieve very high capacities as a result of the low slope.
Blade Mills from McLanahan feature reversible paddles for maximum wear life. The ability to reverse the paddles keeps material in the box for longer, improving retention time. This flexibility is key if producers want to move the unit or feed it larger amounts of deleterious material.
Design elements featured on each McLanahan Blade Mill help keep operation and maintenance simple. A 360-degree section of flights and wear shoes located in the feed end can move material forward, preventing buildup in that area. Screw shafts are made of extra-heavy steel pipe shaft with inner and outer renewable, reversible abrasion-resistant hard iron paddles. Those paddles are preceded and followed by heavy-duty steel flights, equipped with bolt-on inner and outer renewable, abrasion-resistant hard iron paddles. Optional top covers are available, and drive guarding comes standard for personnel safety.
McLanahan offers lab testing for potential Blade Mill users at its in-house testing laboratory.
While Blade Mills are very similar in appearance to Coarse Material Screw Washers, they function much differently. Blade Mills can accept both fine and coarse material, but they are not designed to remove tough, plastic clays. Blade Mills usually work in conjunction with another type of processing equipment, such as a Classifying Tank or wash screen. The major difference between Blade Mills and Coarse Material Washers is that any material and water that enter the Blade Mill must exit through the discharge opening located at the bottom of the box opposite the incoming feed end. Blade Mills have no overflow weir.
When sizing a Blade Mill for your application, consider the following: The type of clay/silt contamination that needs removed. The ore/rock feed size. The tons per hour feed solids capacity. The process flow and equipment location of required washer in your processing plant.
Other equipment that provides scrubbing capabilities include: Log Washers. Coarse Material Screw Washers. Rotary Scrubbers (barrel washers). Trommel or Vibrating Wash Screens. Combination Rotary Scrubber Trommel Screens.
McLanahan Blade Mills feature reversible paddles for maximum wear life.