In most cases, both the Double Roll Crusher and Sizer will accomplish the desired results for many of the same applications; however, there are differences between the two that offer operators greater choices to help meet the requirements of their particular crushing plant.
These differences include the installation, tramp iron protection, roll speeds and method of feeding, drive configurations, product size and, ultimately, cost.
Installation
In practically all cases, the V-belt driven Double Roll Crusher is rigidly mounted to the floor or structure with the feed chute and discharge chute firmly attached. The motor bases are also rigidly mounted to the floor independent of the crusher base mounting.
A McLanahan Double Roll Crusher.
Conversely, the Sizer design incorporates steel wheels into the bottom of the base frame for mounting on rails. The unit can then be rolled out of the material flow, if necessary, to remove tramp material or to perform maintenance.
A flexible connection is utilized between the feed chute and the crusher feed opening to allow for unrestricted movement of the machine. Hydraulic cylinders are offered to raise and lower the wheel assemblies.
A McLanahan Sizer.
Tramp Iron Protection
When an uncrushable item is encountered by a V-belt driven Double Roll Crusher, the movable roll will be forced to move laterally away from the stationary roll. The force exerted by the movable roll will overcome the preset spring tension of the automatic toggle mechanism.
This force causes the toggles to break open, allowing the movable roll to move away from the stationary roll long enough to pass the uncrushable object, then it immediately returns the movable roll to the original position. The crusher remains in constant operation throughout this process.
McLanahan Double Roll Crushers have an automatic toggle mechanism for passing uncrushable material.
Tramp iron protection on the Sizer is provided by an underspeed sensor and fluid coupling on each drive. When an uncrushable object is encountered, the underspeed sensor observes a stall condition and shuts the drives down.
If this does not happen quickly enough, the torque load is increased and the fluid couplings will begin to slip. The fluid coupling slip relieves the stress on the components and therefore, protects the machinery.
In a 100% slip or stall condition, the temperature in the fluid couplings will rise to the temperature limit of the fusible plug, which will effectively disconnect output power. If tramp material has stalled the crushing rolls, production is halted until the tramp is manually removed.
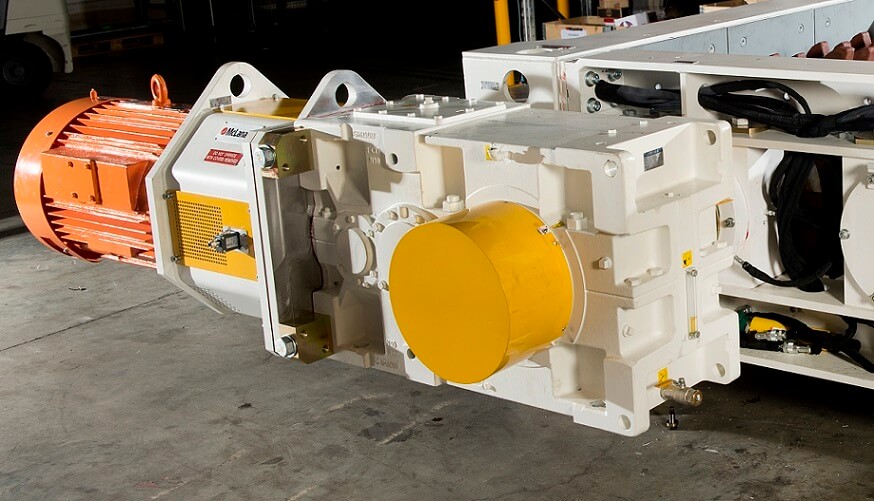
Sizers have a motor, gear reducer, fluid coupling and underspeed sensor, which shuts down the drive in the event of a stall condition.
Drive Configuration
The drive configuration for a Double Roll Crusher consists of motor, V-belt drive and flywheel. The Sizer drive is composed of a motor, fluid coupling and a gear reducer.
The horsepower requirements for a V-belt driven Double Roll Crusher are lower than that of the Sizer due to the utilization of the large flywheels. The kinetic energy stored in the flywheels combined with the higher roll speeds powers the crusher through peak crushing moments.
The Sizer does not utilize flywheels, and the rolls rotate at approximately one-third of the speed of the V-belt driven crusher. Therefore, due to the torque required to perform the crushing action, greater motor horsepower is required.
Roll Speeds and Feeding Methods
A typical 24" diameter Double Roll Crusher has a standard roll speed of 150 rpm. This roll speed can be easily increased to attain higher throughput capacities by changing the electric motor rpm and/or the motor sheave/flywheel diameters. However, with the higher throughput, you run the risk of increased fines generation and accelerated component wear.
One hundred percent of the feed to a V-belt driven Double Roll Crusher must flow between the rolls, creating a ribbon of material and increasing the potential of creating additional fines due to inter-particle crushing taking place. The feed opening spans the length of the crusher rolls but only measures to the centerlines of the roll bodies.
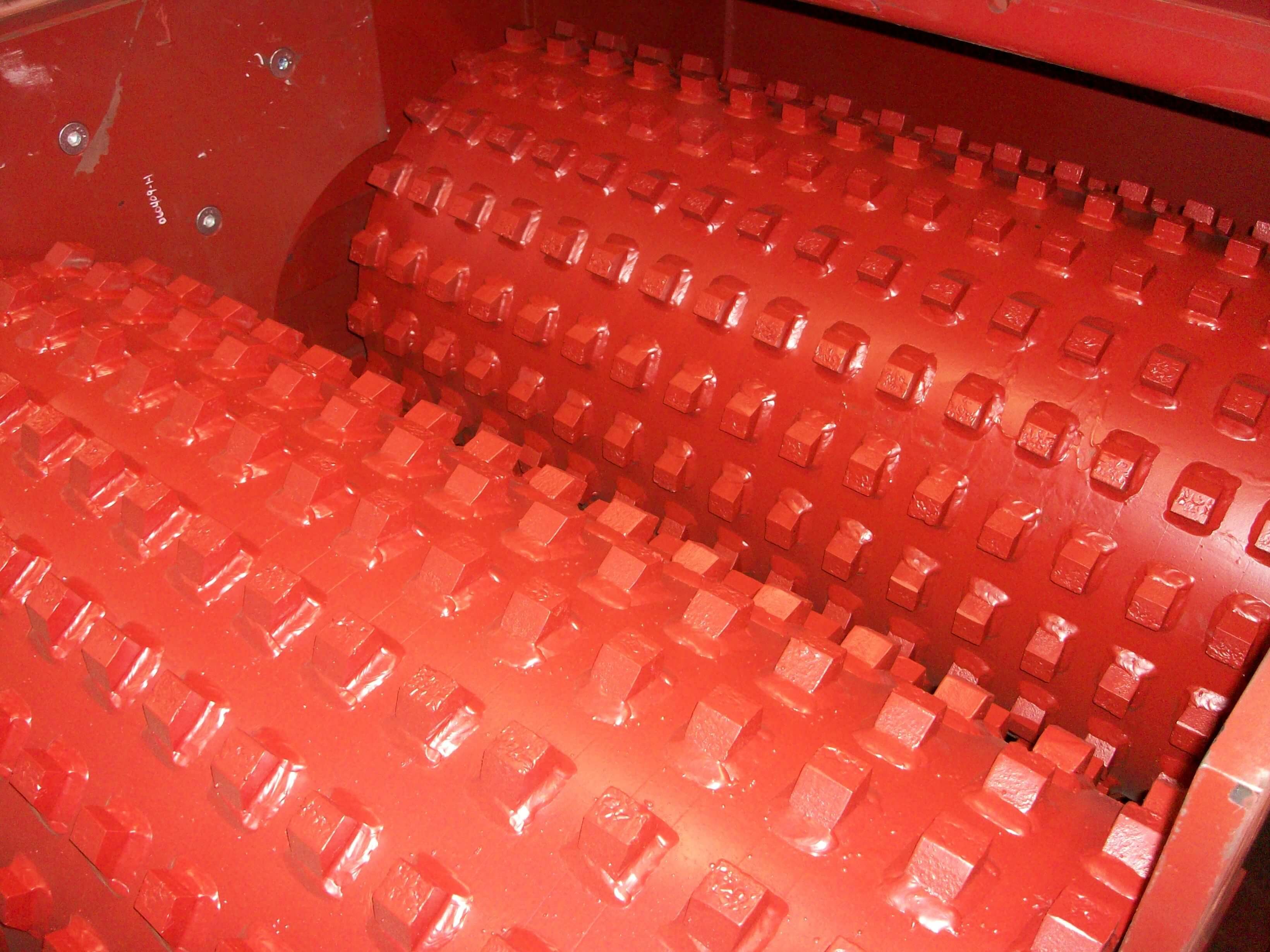
The feed stream flows between the rolls of the Double Roll Crusher.
The rolls of the Sizer rotate at a set speed of approximately 50 rpm (primary and secondary) or approximately 88 rpm (tertiary), which is dictated by the gear reduction of the reducer when powered by an 1800 rpm electric motor. The slower roll speed proves advantageous to component wear life and reduces the amount of fines generated. The larger feed opening also contributes to reduced fines generation and plays a major role in increased throughput capacity.
The Sizer is fed the length of the crusher rolls but also beyond the outer dimensions of the roll bodies, allowing the feed to go between and to the outsides of the rolls, creating three flow streams.
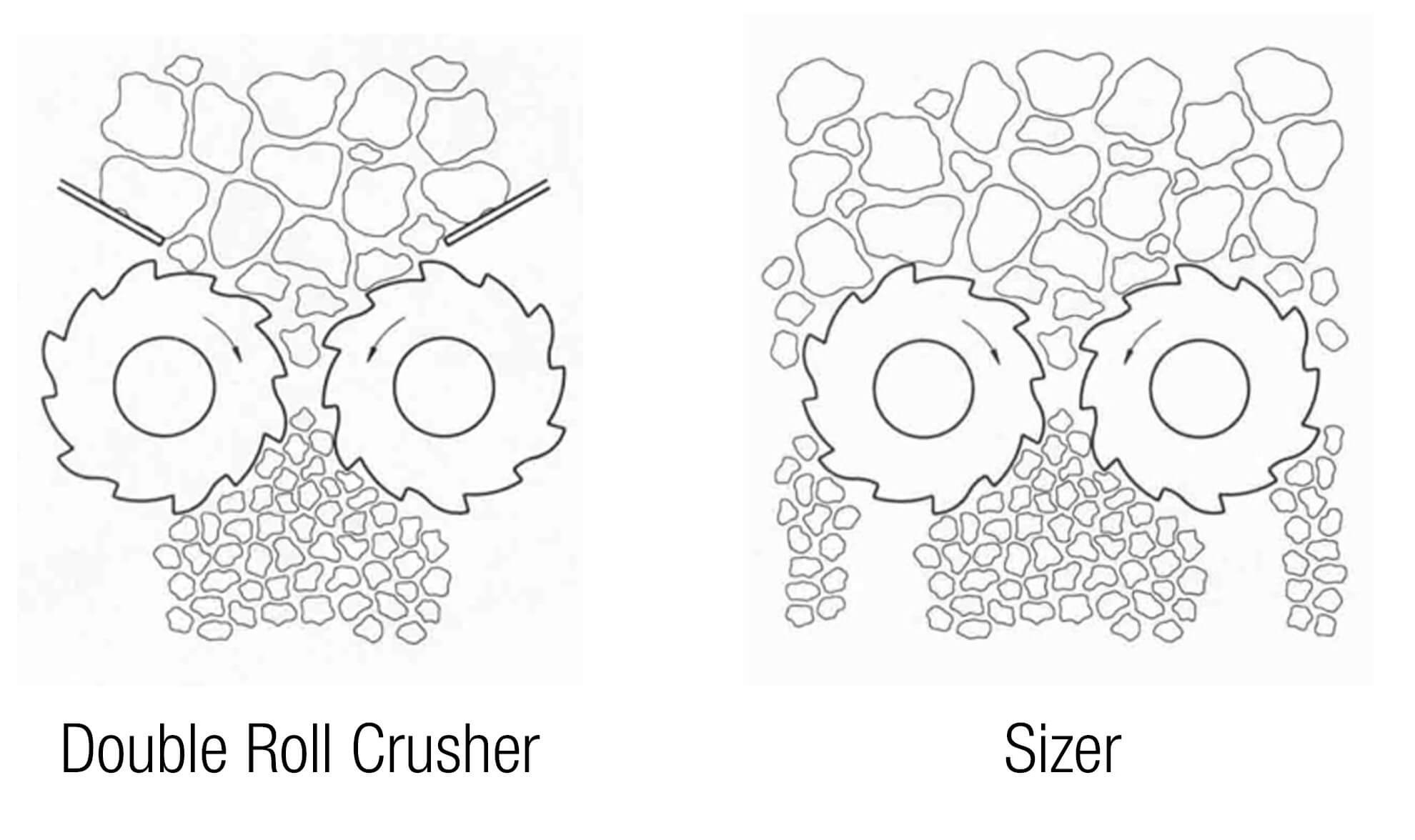
On the outside edge of the Sizer's rolls are sets of replaceable sizing combs that intermesh with the roll teeth. This feature is significant, as it creates a screening effect, allowing most of the undersized material to fall through the crusher without further degradation and also compensates for the slower roll rotation with regard to capacity.
Material is fed across the length of the Sizer rolls so that the feed goes between and to the outside of the rolls.
Product Size
The final product size required is another consideration one must take into account when considering crusher selection. Typically, both machines can produce the same product size until the required product size drops below 1.5” – 2”. It is at this point where a Double Roll Crusher must be used instead of a Sizer. The design of the Double Roll Crusher allows for a finer adjustment and therefore a finer product size.
Cost
With the design differences also comes cost differences. The Double Roll Crusher is the more cost-effective option of the two. The main differences that make up the majority of the cost differences is the drive configurations. Since the Double Roll Crusher is V-belt driven, lower motor horsepower can be used due to the flywheel design.
In comparison, the Sizer is a direct drive, meaning the flywheel has been removed and replaced with a gear reducer, torque limiting coupling and higher horsepower motors. Read more about how McLanahan helped a gold processor with their crushing and sampling circuit.
When deciding between a Double Roll Crusher and Sizer, considering all of these differences will help you choose the right type of crusher for your mineral processing plant.