Primary & Secondary Sizers
McLanahan Sizers are direct drive crusher-sizers that are used in the primary and secondary reduction of friable, low-silica minerals.
Applications
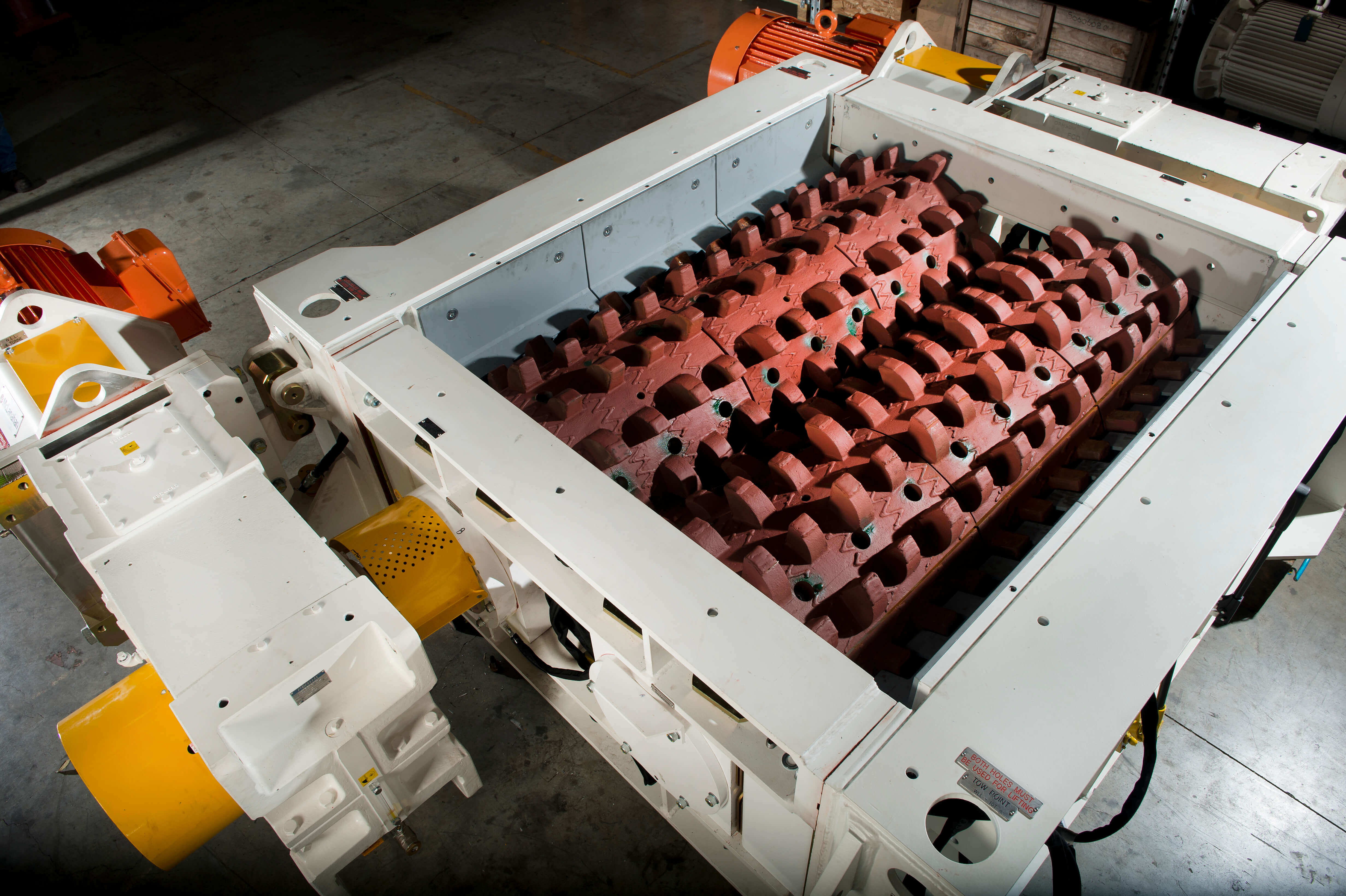
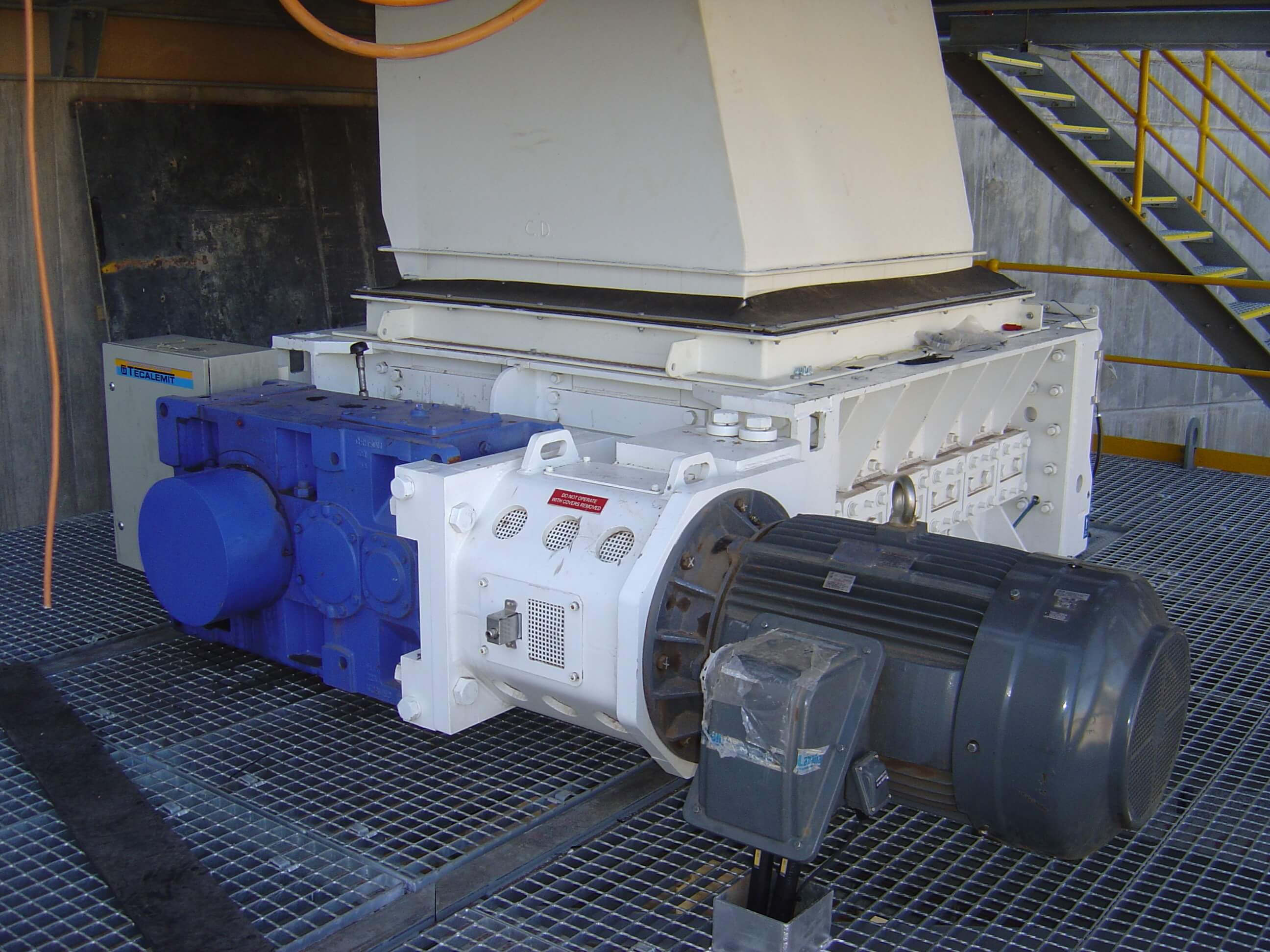
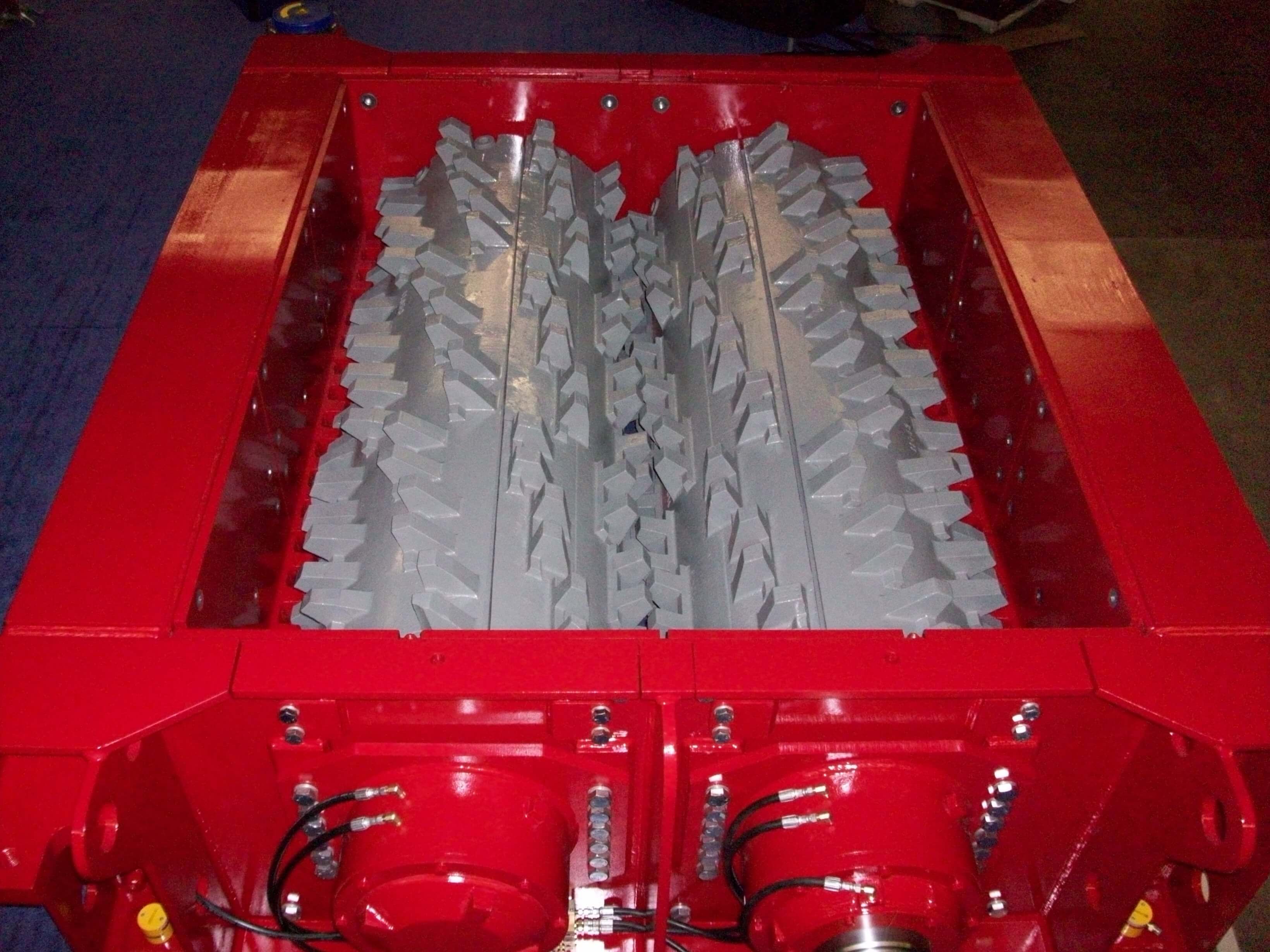
Jump To:
Used in both surface and underground mining operations, McLanahan Sizers can reduce materials such as coal, salt, gypsum, phosphate, limestone, bauxite, petroleum coke, lignite, trona, carbon anodes, oil sands, clay, shale and similar friable minerals.
The direct drive arrangement and low-profile design of Sizers is ideal for movable configurations, such as wheel-mounting for a movable configuration. The preferred method of installation is to mount the unit on rails with a non-rigid connection between the feed and discharge chutes. Because the drives are attached to the mainframe of the sizer, it is possible to roll the entire unit out from under the hopper or material stream when maintenance is required.
Sizers have long been used in a variety of applications, including ROM feeds, coal, salt, gypsum, phosphate, limestone, bauxite, petroleum coke, lignite, trona, carbon anodes, oil sands, clay, shale and other friable minerals.
Primary and Secondary Sizers are sized and selected based on the specific material and lump size to be crushed. Tooth profile selection allows the material to be grabbed and pulled into the crushing zone for maximum efficiency.
Sizers use an electric motor to drive the gear reducer, which is mounted directly to the crushing shaft. The motor is protected via a fluid coupling fitted with a thermal element to eliminate the risk of shock loads or stall events transferring through to the motor. Inward rotating rolls on primary and secondary sizers allow under-sized feed material to flow around the crushing zone and backside of the inward rotating rolls. The intermeshing sizing combs prevent any oversized material from passing through. This creates a screening effect and minimizes additional fines generation, which can be created through inter-particle crushing.
Sizers have a direct drive arrangement and low-profile design that allows wheel mounting for a movable configuration. The preferred method of installation is to mount the unit on rails with a non-rigid connection between the feed and discharge chutes. Since the drives are attached to the mainframe of the sizer, the entire unit can be rolled out from the feed stream to facilitate maintenance. McLanahan Sizers are equipped with hydraulic lift cylinders for ease of wheel activation.
With Sizers installed and operating around the world, McLanahan is one of the world's most experienced manufacturers in the design and production of sizers. These sizers are designed and manufactured to improve the total cost of ownership over the life of your machine by being more efficient and easy to maintain. McLanahan provides lifetime service and support of Sizers and uses standard, readily available motors, gearboxes and couplings. All segments and sizing combs in McLanahan Sizers are designed to be interchangeable throughout the machine.
Primary and Secondary Sizers feature a unique hydraulic product size adjustment, which allows producers versatility if the product size requirements change. This feature allows producers not only the option of maintaining original size specifications, but also gives them the ability to adjust to meet changes in product size requirements. The hydraulic adjustable roll also allows producers to maintain product specifications when compensating for tooth wear.
If your Sizer is operating with worn teeth, its throughput capacity will be reduced. To keep your crusher operating at maximum efficiency, monitor the height of the teeth by comparing them to the original as supplied tooth height and applying hardface welding where needed to build up the teeth.
Controlling the flow of feed material into a sizer guarantees an even distribution along the full length of the rolls and an even feed split between the rolls. This ensures even wear of both rolls, as well as even wear along the length the rolls. This helps to maximize wear part life and throughput capacity of the sizer.
Check the Lubrication Section of the Installation, Operation and Maintenance Manual for the specific quantity, but you want to be sure you are adding enough new grease to remove all the used grease from the seal.
To change the oil in the Sizer gearbox, first remove the top inspection cover. Inspect the internal components for damage, debris or wear. Remove the desiccant filter/breather and replace it with a new one. Fill the gear reducer until it reaches the fill level on the sight glass.
McLanahan Sizers reduce material with minimal dust and fines generation.