Sampling Jaw Crushers
Sample Jaw Crushers feature the same operating principles and robust design associated with larger Jaw Crusher offerings, in a more compact, lower feed rate configuration that is well suited to Sampling System and Pilot Plant crushing applications.
Applications
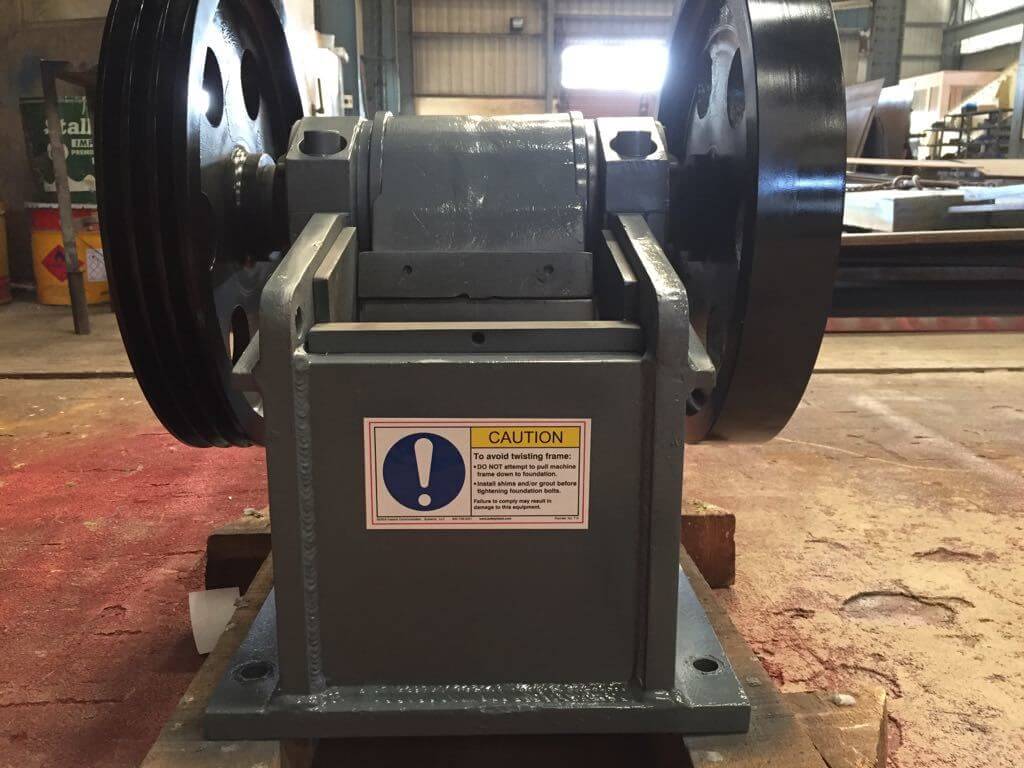
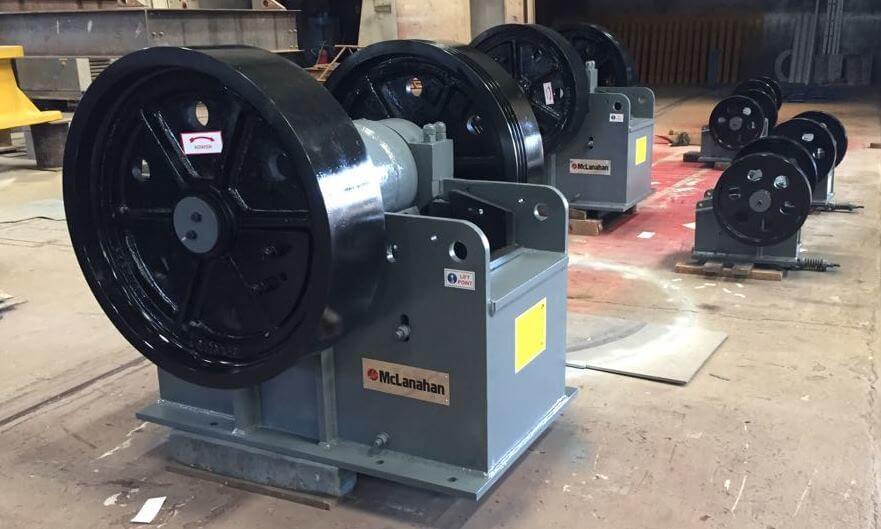