Tertiary Sizers
Tertiary Sizers can be used in surface and underground mining operations for the tertiary reduction of friable, low-silica materials, such as coal, salt, gypsum, phosphate, limestone, bauxite, petroleum coke, lignite, trona, carbon anodes, oil sands, clay, shale and more.
Applications
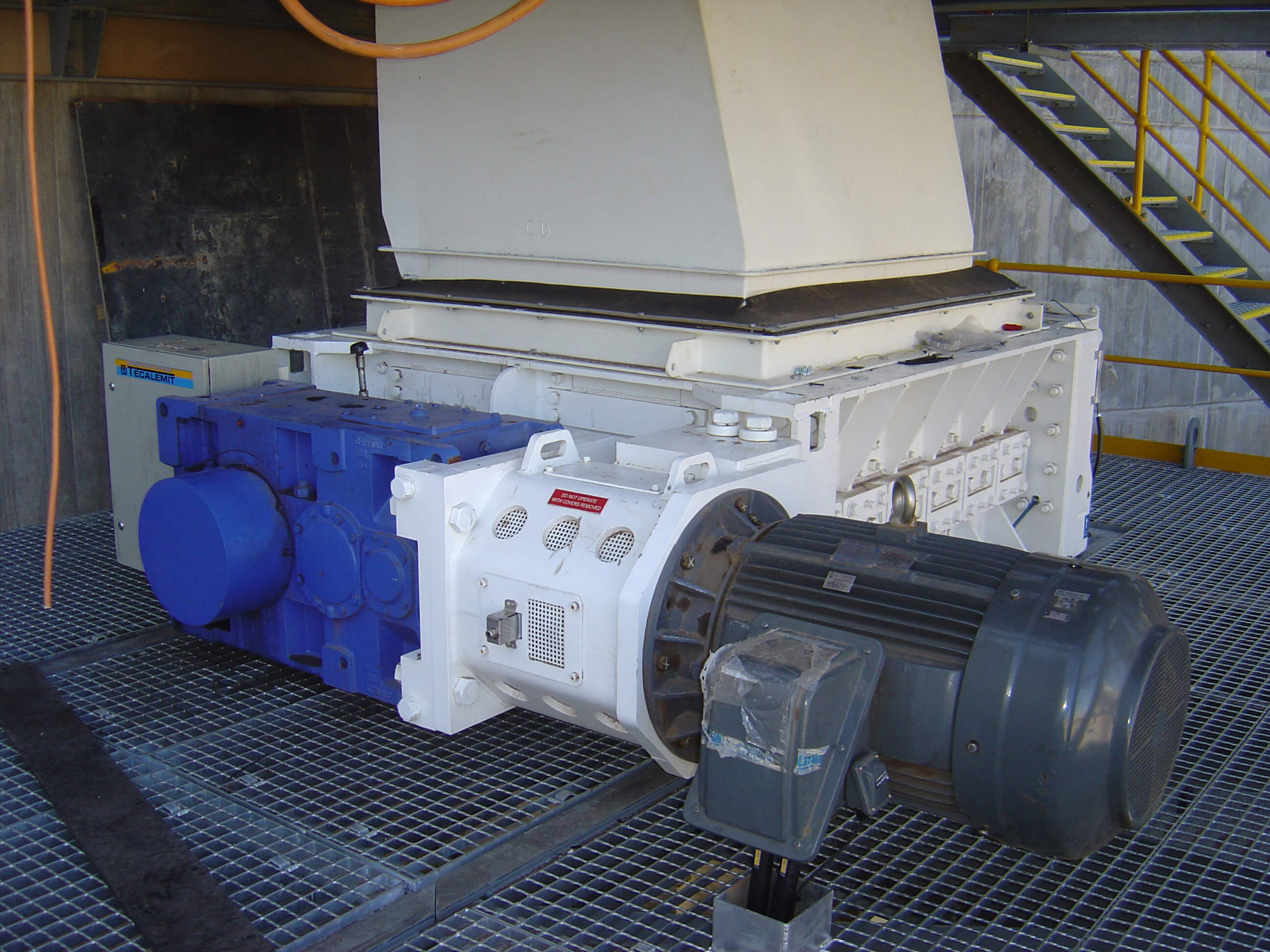