Thickeners
Thickeners — or Clarifiers, depending on the application — can be used to recover immediately reusable process water, as well as extract fines and other materials. Thickeners are used by mineral and aggregate producers, as well as by environmental contractors in industries such as wastewater management, to separate solids from liquid in a slurry.
Applications
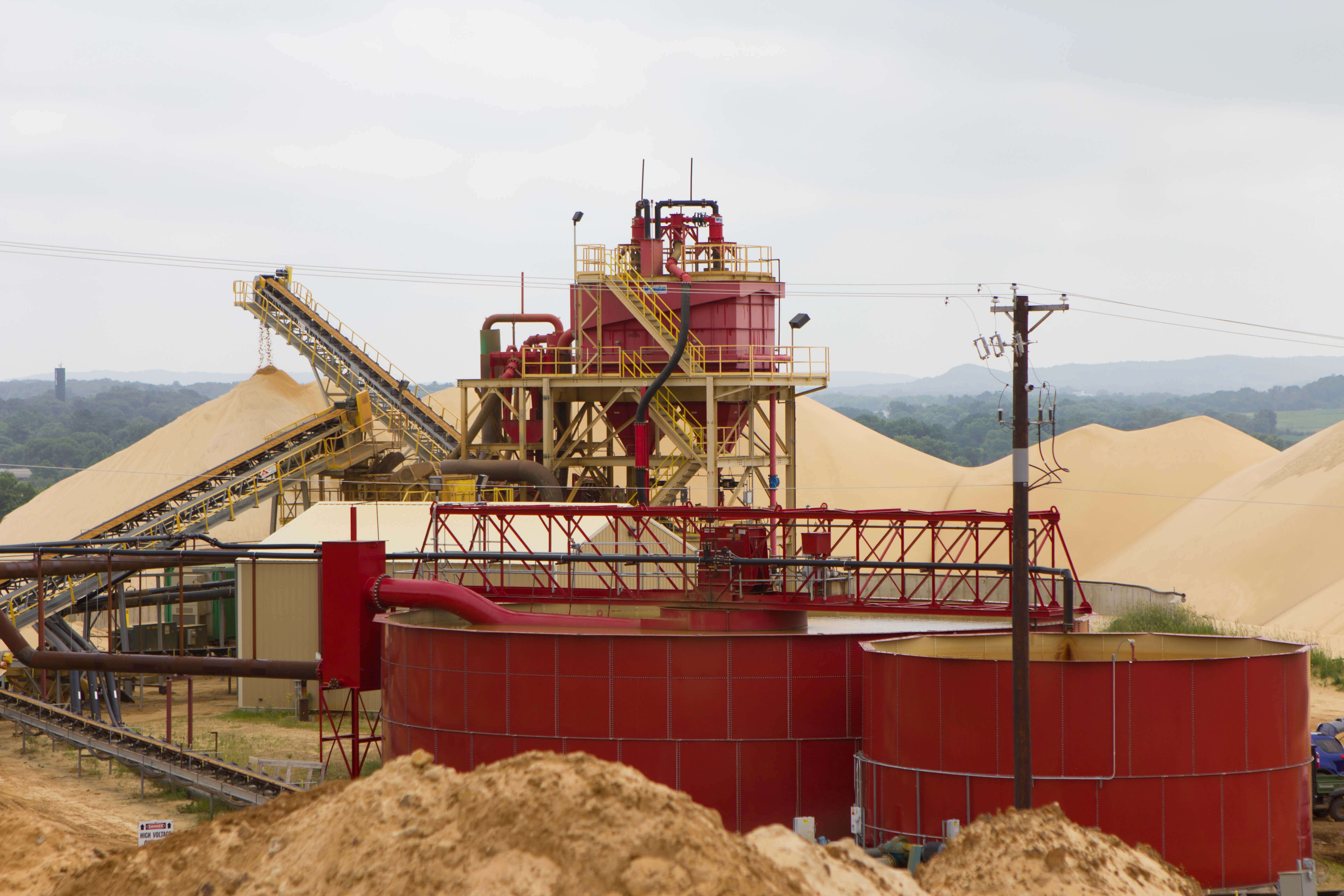
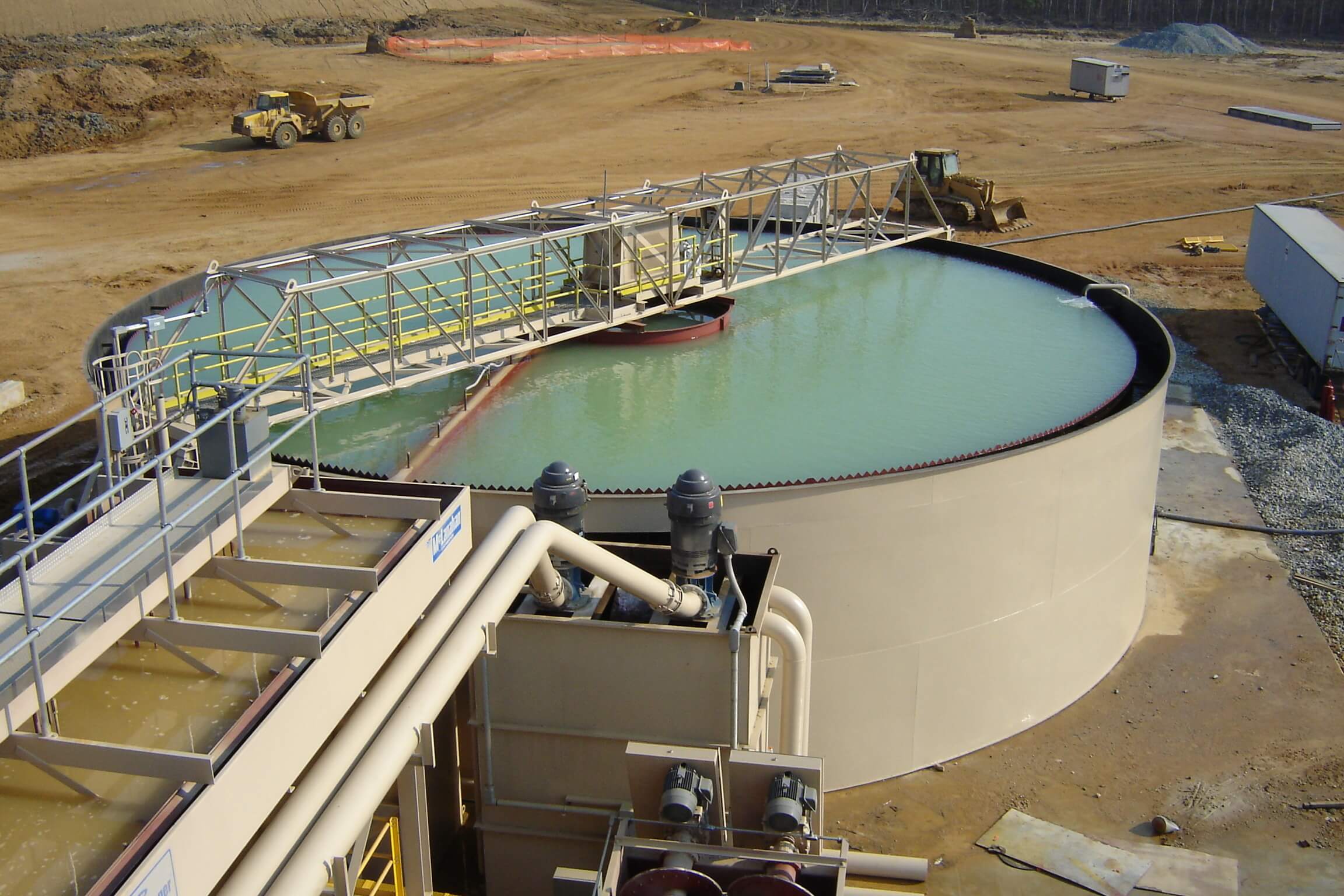