Multi-Stage Sampling Systems
Multi-stage sampling refers to sample processing equipment, structure, buildings, etc. that make up a complete sampling solution following the primary stage of sampling equipment.
Applications
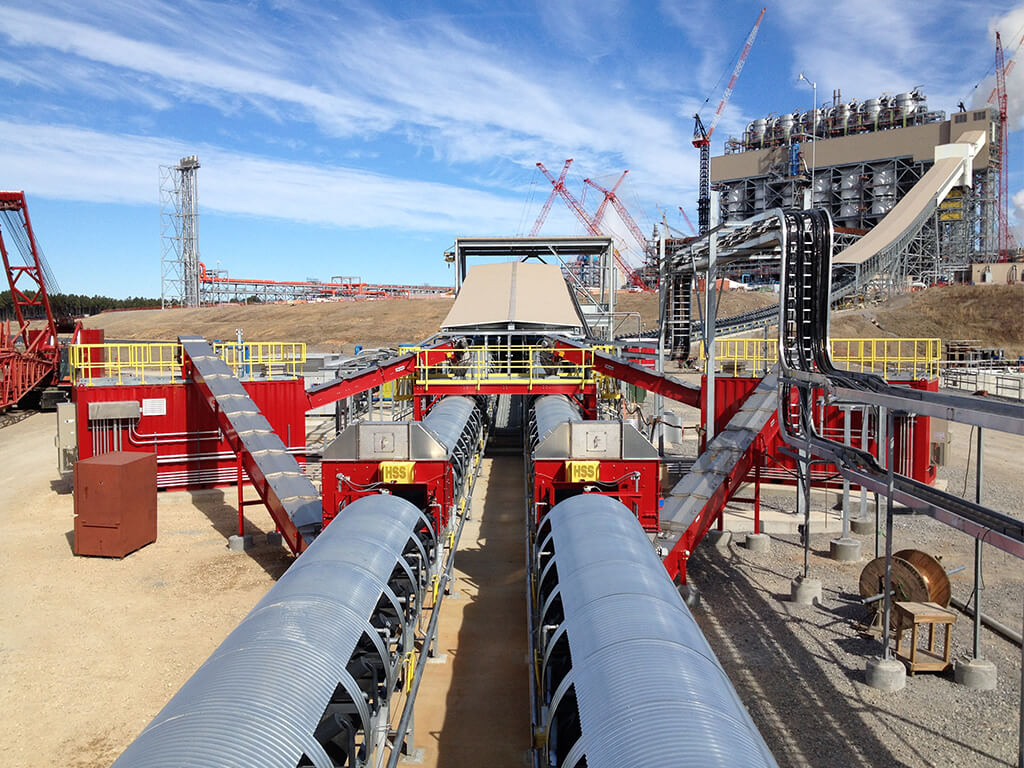
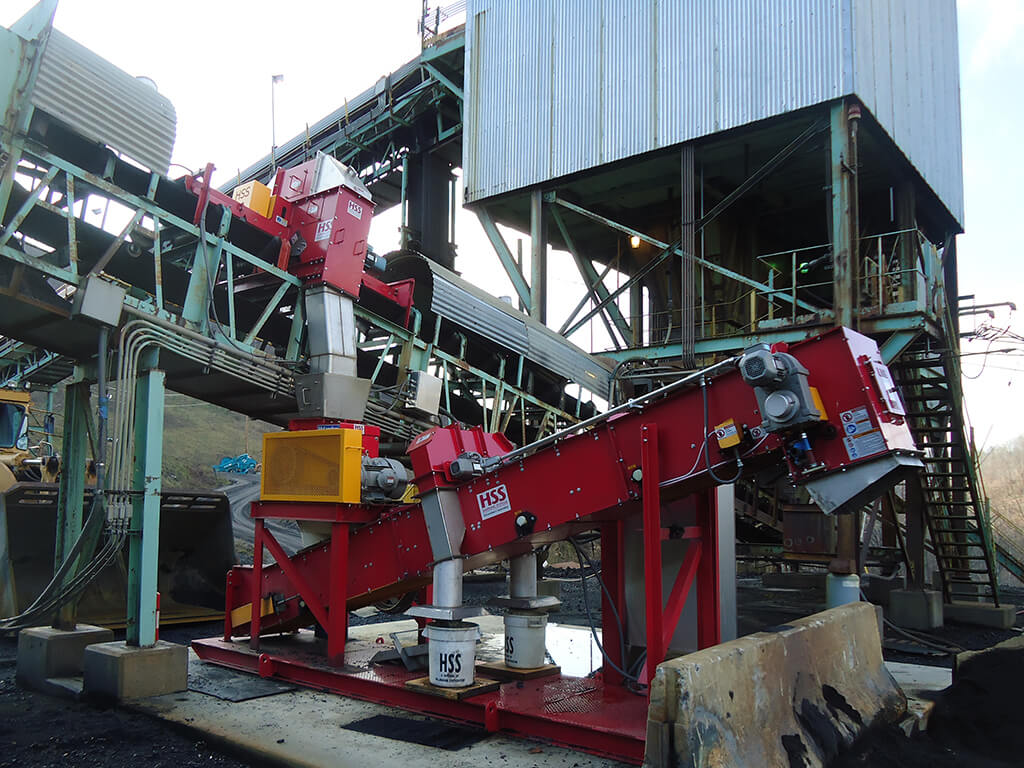
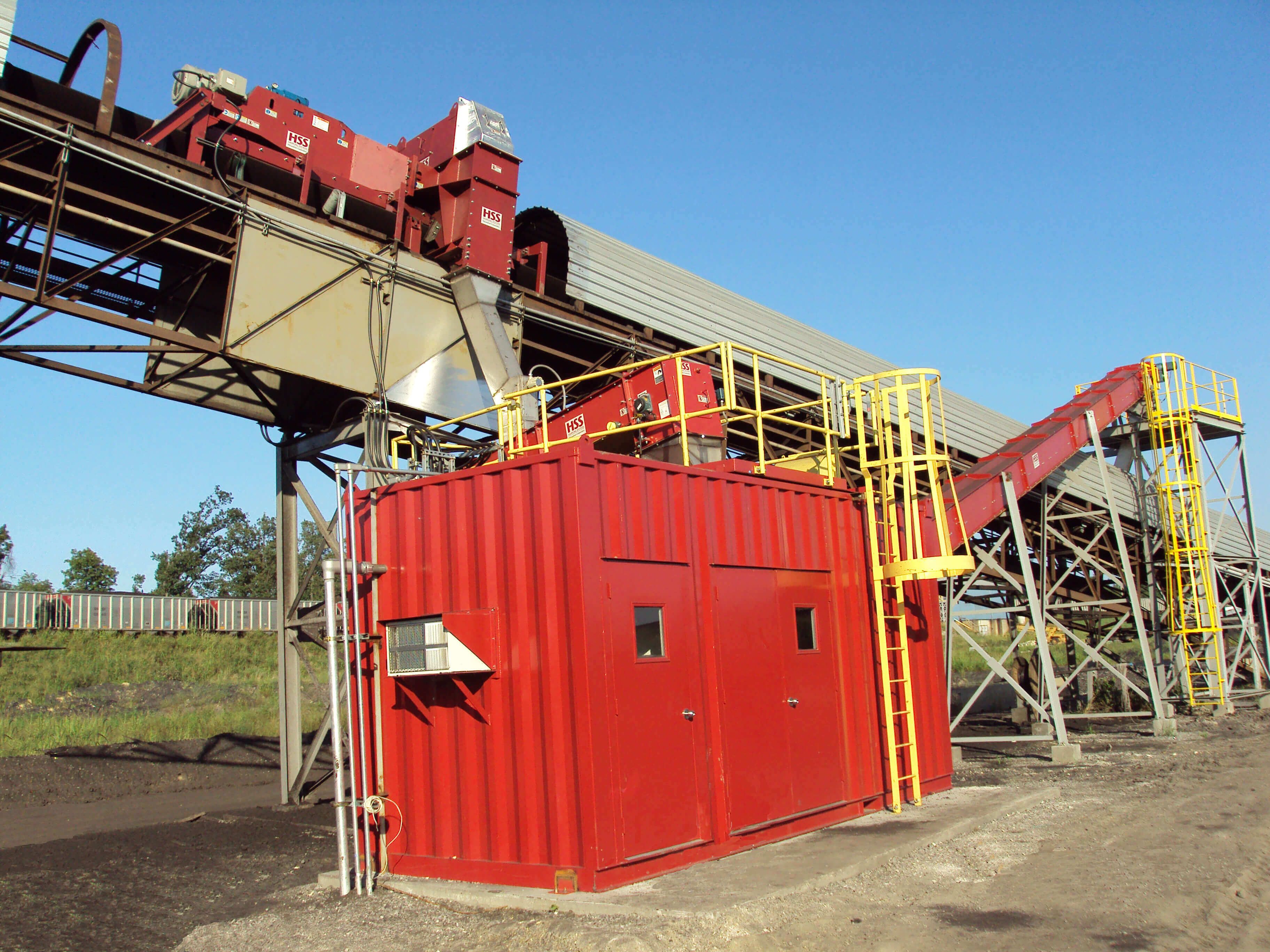
Multi-stage sampling refers to sample processing equipment, structure, buildings, etc. that make up a complete sampling solution following the primary stage of sampling equipment.
Applications
Jump To:
In sampling applications, minimum sample mass collected at the primary stage of sampling is often too large to handle in a practical, cost-effective manner. Handling large sample masses typically requires more sample collection capacity, more frequent emptying or replacement of sample collection containers, lifting devices or equipment to handle sample collection devices, larger offline laboratory equipment to process samples, and excessive amounts of material to dispose of once the lab has finished its processing work. These issues, as well as others not specifically mentioned here, add downstream costs to a quality program.
The solution to these difficulties is to handle as much processing of primary samples as is practical within a mechanical sampling system. A complete mechanical sampling system, or MSS as they are often called, can consist of a number of different types of equipment that may not be limited to sampling equipment. Other mechanical sampling system equipment frequently used includes crushers (hammermills, jaw crushers, roll crushers), conveyors, mixers, dividers, and multi-station collectors, to name a few common machines. A complete mechanical sampling system will incorporate as many types of sampling equipment as necessary to meet the needs of the application and satisfy layout requirements, while also attempting to minimize the total number of pieces of equipment. More handling and transferring of samples introduces more potential sources of error into the sample collection and handling process.
At the end of the day, the goal of a sampling program is to represent a relatively large amount of material with a relatively small amount of sample. More sample collection and processing completed within a mechanical sampling system, in an automatic fashion, will result in a more correct, efficient, and cost-effective sampling program.
A common example of a multi-stage sampling system offering is a sampling system installed in a modular sample building — a custom designed and fabricated building that is intended to house a number of equipment configurations in a prepackaged semi-portable system. This modular building arrangement often includes a sample crusher, reject conveyor, secondary sampler and sample collection — mechanically and electrically installed prior to shipment.
Other features include lighting, power outlets, local jog and stop operators, a separate control room with HVAC, and heating and ventilation in the equipment portion of the building. Additional options are available, such as a building top access platform (field assembly required), exterior lighting, and a separate sample feed conveyor (if needed per the system layout).
Assuming a sample feed conveyor is included, primary sample would be directed from the discharge of the primary sampler to the inlet of the sample feed conveyor. The sample feed conveyor is usually installed on top of the building if space permits, but it can convey material from wherever the primary sample is located to the roof inlet of the sample building. Sample material is fed from the sample feed conveyor at a controlled rate to the sample crusher (located inside the building) where the particle size is reduced as necessary. The crusher discharges into the reject conveyor inlet where it is spread out along the conveyor belt for a uniform flow at a uniform cross section to the secondary sampler. The secondary sampler removes final sample increments from this material flow for collection in whatever sample collection device is provided, while the remaining material continues up the reject conveyor and out of the building. The rejects are then removed by whatever rejects handling system has been designed with the sampling system.
Many other system configurations exist, and can use many types of equipment in a wide variety of configurations. The ultimate goal in any sampling application is to collect smaller secondary (or tertiary, quaternary, etc.) samples for analysis, including crushing stages if needed.
Some popular application for Multi-Stage Sampling Systems include:
Sampling requires a relatively small amount of material be collected to accurately represent a relatively large amount of material. How exactly this is accomplished can vary for any number or reasons. The reasons can range from the type of material handled, to the industry in question, to the constraints imposed by physical layout requirements, to the specific needs of a client’s sampling program.
Suffice to say that being successful requires a complete understanding of each application and close attention to many details. The success of a sampling installation requires that these details be addressed in a way that complies with relevant sampling standards and theory, best practices in sampling and material handling, and experience implementing successful sampling systems. McLanahan learns the needs of each client, understands the details related to sampling, and applies specific sampling and material handling knowledge into a sampling system that results in a cost-effective sampling solution that seamlessly integrates into a client’s facility.
When you work with McLanahan to build your complete multi-stage sampling system, a sampling specialist will take the time to learn about your facility, application, and sampling needs. After fully understanding your application requirements, McLanahan can offer advice on equipment options, system layout, and sampling plans and then put together an appropriate solution.
McLanahan Modular Sample Buildings are pre-packaged Multi-Stage Sampling Systems housed in modular-style structures. These units are tailored to each application but will typically include a Sampling Crusher (such as a Sampling Hammermill Crusher, Sampling Jaw Crusher or Sampling Roll Crusher/Sizer) and a secondary Sampling System (such as a Cross Belt Sampler or a Falling Stream Sampler). The modular-style of this type of Multi-Stage Sampling System allows for quick and easy setup on site, as well as a reduction in installation costs.
Not necessarily. This will depend on a number of things, but primarily it would be based on the needs of your application and your budget. Some applications require only relatively small amounts of sample be collected during the primary sampling stage. In these cases, it doesn’t always make sense to incorporate the additional equipment to reduce the sample within the mechanical sampling system. Sample material from the primary stage would simply be collected and taken to the lab for processing.
Other times, larger and potentially cumbersome amounts of material are collected at the primary stage, but a customer does not want to commit the capital to purchasing additional equipment to automatically process sample after the primary stage. In this case, sample would be manually reduced (and possibly crushed) by lab personnel. Reject material would then need to be manually disposed of as well. Usually, if larger amounts of primary sample are needed, additional equipment is purchased to crush and reduce the primary samples to a reasonable amount that the lab can easily handle and process. This scenario does have a higher capital cost, but it will ultimately prove to be less expensive, as a significant amount of manual handling is eliminated. As is often the case, the best way of handling a situation is application specific. This is why McLanahan encourages prospective clients to contact us to discuss their sampling needs so we can learn about your application and offer advice tailored to your specific requirements.
Multi-stage sampling systems are incorporated in numerous types of applications across a wide variety of industries.