Introduction
Sampling ensures an end product is meeting specifications as-produced, as-shipped or as-received. In addition, sampling can be used to measure plant performance. The practice involves collecting a small portion of a bulk material to reflect the larger group of material for analysis.
While the analysis will provide the data necessary to determine if the product is in spec or the processing plant is operating optimally, collecting the sample accurately and precisely is equally important to providing a correct analysis of the product as a whole. Samples can be collected either manually or automatically.
Automatic vs. Manual Sampling
Manual sampling requires quality control personnel to physically collect the sample from the material stream. There are several different methods used for manual sampling, including:
- Stopped belt sampling, which involves collecting a section of material from a stopped conveyor belt
- Stockpile sampling, which involves collecting a sample of material directly from the stockpile
- Transfer belt sampling, which involves collecting the sample at a transfer point, such as from one conveyor to another
Each of these methods has challenges in terms of sample accuracy and difficultly of the collecting procedure. Because all of these methods require personnel to be near operating equipment and flowing materials, safety is of the utmost concern.
Automatic sampling, on the other hand, reduces the safety risk by removing personnel from the equation. This method of sampling uses Mechanical Sampling Systems that are automated to collect a representative sample of material precisely and accurately.
In addition to safety, Mechanical Sampling Systems can be used for:
- Improved accuracy
- Better repeatability
- Improved efficiency
- Lower long-term sampling costs, particularly indirect or hidden costs
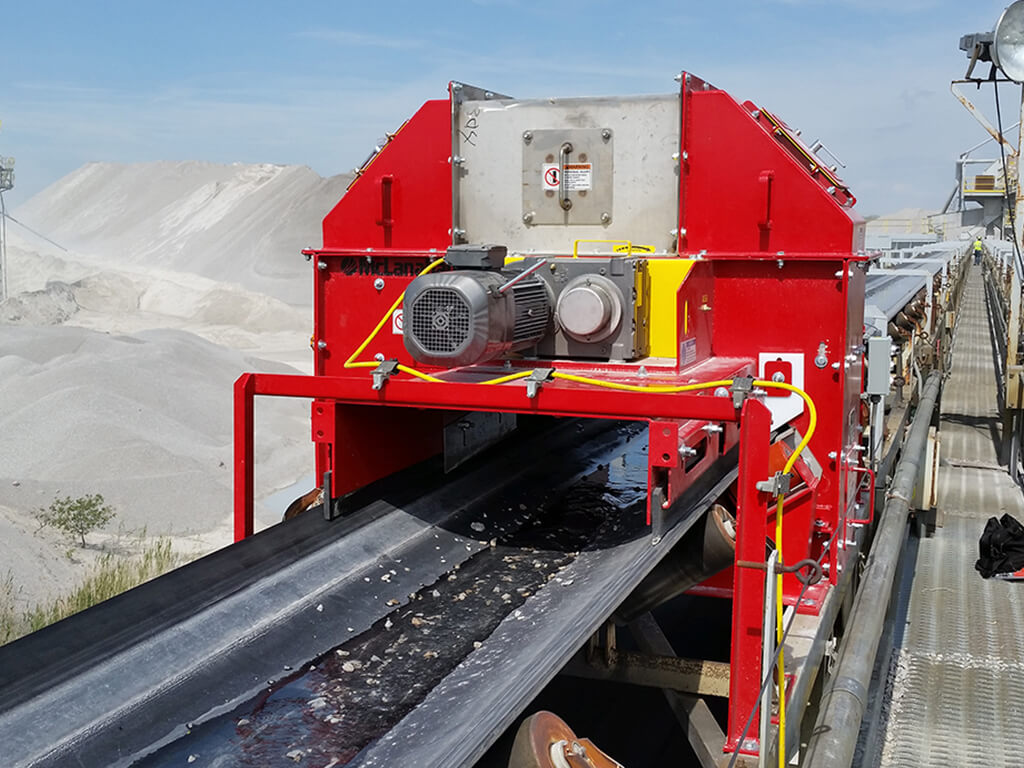
What Are Mechanical Sampling Systems?
Mechanical Sampling Systems are automated processes for collecting representative samples from a conveyor belt, falling stream or fixed point.
These machines can be used to process nearly any dry bulk material, including:
- Bauxite
- Coal
- Iron ore
- Petroleum coke
- Phosphates
- Precious metals
- Sand
- Salt
- And more
Types of Mechanical Sampling Systems
There are several types of mechanical sampling systems, including:
- Auger Sampling Systems
- Cross Belt Samplers
- Falling Stream Samplers
Auger Sampling Systems
Although sampling from flowing streams of material is preferred in order to collect the most representative sample, this isn’t always possible.
Auger Sampling Systems are a type of Mechanical Sampling System used to collect material from a fixed point, such as from a stockpile, truck, railcar or other container. This type of sampling system is particularly useful in as-shipped or as-received applications where the material is confined to the shipping container.
An Auger Sampling System consists of a vertical spiral shaft that rotates in a pipe. The bottom of the spiral shaft extends past the pipe and contains a cutting head that loosens material to be conveyed up the pipe toward a collection hopper at the top.
Auger Sampling Systems are typically found in the following applications:
- Coal
- Coke
- Crushed Ores
- Metal and non-metal concentrates
- Potash
- Salt
- Wood Pellets
Cross Belt Samplers
Cross Belt Samplers, also known as sweep samplers, collect a sample increment by rotating a counterweighted sample cutter perpendicularly through a moving material flow on a conveyor belt.
This type of mechanical sampling system is a simple and cost-effective solution to collecting stopped belt-like sample increments without interrupting plant operations.
Cross Belt Samplers are common in aggregate, sand, stone, coal and salt applications. Other applications in which Cross Belt Samplers are common include:
- Biomass and alternative fuels
- Coke
- Concentrates
- Ores – copper, nickel, bauxite, gold, silver
- Phosphates
- Potash
- Power generation
- Steelmaking
Falling Stream Samplers
Falling Stream Samplers include a wide range of designs. The key characteristic of all of these designs is that the sample material is collected from a main process flow that is either in a free-falling condition or traveling through some trajectory, such as at the discharge of a conveyor.
These type of samplers tend to be simpler in design and functionality. They usually offer highly reliable operation and relatively low maintenance requirements. Falling Stream Samplers are well suited to high flow rate applications where minimal downtime is a requirement, such as load-out systems.
Falling Stream Samplers can have some limitations. Depending on the style of Falling Stream Sampler being considered, the sampler type usually requires a larger vertical clearance for installation, and it is usually more invasive and expensive to install.
Applications where Falling Stream Samplers are common include:
- Aggregates
- Base metals
- Bauxite
- Coal
- Coke
- Concentrates
- Copper
- Crushed ore
- Gold
- Gravel
- Iron
- Mineral Sands
- Potash
- Salt
- Sand
- Potash
Bottom Dump Samplers
Bottom Dump Samplers are one type of Falling Stream Sampling System. They feature a sample cutter that passes through the moving material flow at a constant speed while collecting material inside it. The cutter releases the material back into the main flow once it reaches the opposite side of the material stream. The cutter then passes back through the material flow to the original parked position, where it will discharge or dump the sample increment into a discharge chute.
Bottom Dump Samplers can feature an overhead carriage design or a horizontal carriage design.
Vezin Samplers
Vezin Samplers are a fully enclosed type of Falling Stream Sampler. Inside, they feature a rotating sample collection assembly with sample cutters that pass at a consistent, uniform speed through a falling stream of material that enters through the top of the unit. The collected sample discharges through a chute to the next part of the sampling process, while the reject material passes through the sampler.
Multi-Stage Sampling
Mechanical Sampling Systems can have a wide variety of configurations depending on the needs of the application and include several samplers (and even Sample Crushers) in a Multi-Stage Sampling System arrangement.
For example, a primary sampler used to remove a sample from a main process flow would be considered a one-stage sampling system. A primary sampler discharging a sample to a secondary sampler would be considered a two-stage sampling system.
Multi-Stage Sampling reduces the representative sample size even further to decrease handling before, during and after lab processing. Most Multi-Stage Sampling Systems require crushing, which can be accomplished with small-scale types of crushers used in product applications.
Types of Sampling Crushers
Sample crushers look and function the same way as their larger counterparts, only they are specifically designed to handle low-tonnage applications, such as sampling. Types of Sampling Crushers can include:
- Sampling Cone Crushers
- Sampling Jaw Crushers
- Sampling Hammermill Crushers
- Sampling Roll Crushers/Sizers
Sampling Cone Crushers crush material between a wobbling mantle (moving piece of steel) and a concave (a stationary piece of steel). The particles are squeezed and compressed as they make their way down the crushing chamber until they are small enough to discharge from the bottom of the machine.
Sampling Hammermills fracture material upon its impact with a rotating hammer bar inside the crushing chamber. The fractured particles are drawn farther down in the crushing chamber, where they are further reduced against crushing screens.
Sampling Jaw Crushers crush material between a moving piece of steel and a stationary piece of steel that form a V-shaped crushing chamber. The material is squeezed and compressed until it is small enough to discharge out the bottom of the chamber.
Sampling Roll Crushers/Sizers crush material between two rotating rolls or between a roll and a breaker plate. Sized material exits out the bottom or the machine.
How to Choose a Mechanical Sampling System
The types of sampler(s) used in an application can vary based on the following factors:
- Industry
- Material, including size and bulk density
- Geographic location
- Plant layout
- Plant operations
- Preference
The right sampling solution for an application will take all of these factors into account, as well as the goals and concerns of all parties involved in the sampling process. This can include operators, end-users, testing companies, sampling consultants and engineering firms.
Developing a sampling solution involves a thorough understanding of the application, particularly the needs and goals associated with sampling.
Benefits of Mechanical Sampling Systems
Mechanical Sampling Systems have many benefits over the alternative of manual sampling, including:
- Limiting personnel exposure to operating equipment
- Minimizing manual material handling requirements
- Eliminating human discretion in sample collection
- Reducing potential human error in the sampling process
- Correctly determining the composition of a material
- Correctly valuing as-shipped or as-received material
- Automated collection, crushing and reduction of samples
- Ensuring the product specifications are met
- Ensuring contract requirements are met
Automated sampling with Mechanical Sampling Systems is significantly more efficient than manual sampling, and it offers better results in most cases. Mechanical Sampling Systems may not contribute to the production of an end product, but they are crucial to correctly valuing that product and ensuring the plant is operating correctly. Correct sampling and quality sampling equipment allow for an organization to better understand and streamline their operation.